Blog What is Sand Casting and How Does It Work?
By: Dave Olsen
Sand Casting
Sand casting can be traced back to earlier than 1000 B.C. It is widely accepted as the oldest known casting process. The sand-casting process has evolved significantly since the beginning. But the process of how to sand cast has not strayed.
The cast molding process is basic, create a cavity in the shape of the part you want and pour molten metal into it. For sand casting beginners, the process is referred to as sand casting because the mold that contains the cavity, into which metal is poured, is made of compressed or compacted sand. The sand does contain other materials that encourage it to hold shape.
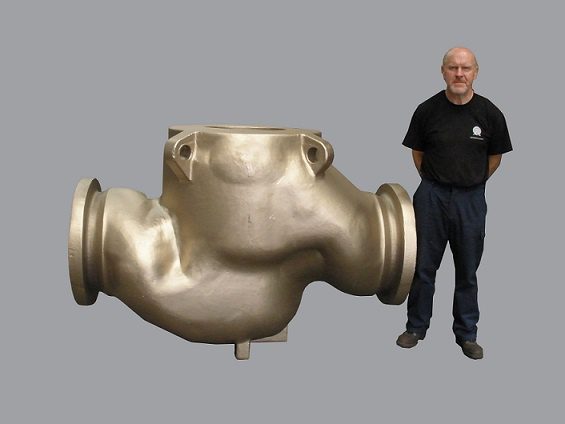
Sand casting is the most versatile and arguably most widely used metal casting method, after centuries of development. Design requirements (including shaping and dimensional needs), piece and tooling cost, quantity needed, and even feasibility to manufacture dictate which metalworking processes (including which casting processes) are most suitable.
Product manufactured using sand casting employ techniques that produce shaped parts of nearly any design, including very large parts and those with internal passageways. There may be more optimal casting or metalworking processes for any specific product based on:
- Needed tolerances
- Design intricacy
- Volume
- Tooling availability
- Lead time
It is likely that a casting in the needed configuration could be made using the sand-casting process. Learn more about how to sand cast and the cast molding process below.
The Sand Casting Process Steps
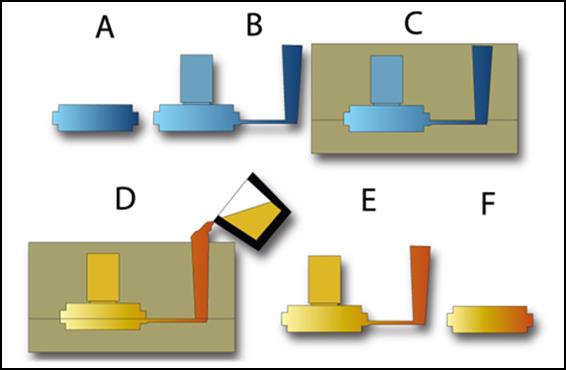
A. Producing the Pattern – Desired product
- The cast molding process utilizes a reusable pattern with the same details as the desired finished part. There is an allowance for thermal contraction or shrink.
B. Producing the Pattern – Gates and risers: The metal delivery system
- The pattern produced in step “A” also includes the metal pathways that will feed the desired cast product design with appropriate gating and risers. This drives the inevitable thermal contraction to acceptable areas – someplace other than the actual desired finished product. It also manages the metal flow and needed gas venting.
- Patterns are made of many different materials such as wood, metal, synthetics, expandable polystyrene (EPS), and others depending on needed volume and tolerance.
C. Creating the mold
- A refractory material which is stable at high temperature (sand, in our example) is formed around the pattern. The material must be strong enough to hold the weight of the molten metal during casting and resistant to reaction with the metal, yet brittle enough to be readily broken away from the solidified metal after the casting cools.
- There are a variety of sand materials that can be used to make the mold. The sand typically includes other materials like clay or some chemical bonding agent to strengthen it so that it will stand up to the pouring process.
- Alternatively, the mold may be created by machining the desired shaped cavity directly into a block of sand. The technique is widely used during product development because design changes may be managed and implemented quickly, or for parts with infrequent usage to avoid the storage or maintenance of a physical pattern.
- The mold is typically produced in two pieces, the top half or “cope” and the bottom half or “drag”. Once the sand has set (using the traditional/non-machined process), the halves are separated, and the pattern removed. A refractory coating is added to provide a better surface finish and protect the mold from the turbulence of the poured metal. The halves are placed back together, leaving a cavity in the shape of the pattern.
- The mold may also include cores, a method that is used to produce desired internal passageways in the final product.
D. Pouring the metal into the mold
- Molten metal is poured directly into the static mold. It fills the cavity that defines both the finished part and risers. The risers feed the casting with an available supply of liquid metal. As they are designed to cool and solidify last, the shrink, and potential void, is concentrated in the riser rather than in the desired part.
- There are several variations of “tilt pouring”. It is a process designed to allow metal to flow more smoothly into the casting, eliminating turbulence. Less turbulence can help prevent the creation of oxides and casting defects.
- Virtually any alloy can be produced using this process. For those materials particularly reactive with oxygen, a procedure such as argon shielding may be employed to keep air away from the molten metal.
E. Shakeout
- The casting, including both the desired part and the additional metal needed to create it, solidifies and cools. The sand is broken way in a shakeout process.
- Much of the sand used to create the mold is captured, reconditioned, and reused.
F. Final operations
- The gates, runners, and risers are cut from the casting, and if necessary, final post-processing sandblasting, grinding, etc., are performed to finish the casting dimensionally. Sand castings often require at least some additional machining to reach final dimensions or tolerances.
- Parts may be heat-treated to improve dimensional stability or properties.
- Non-destructive testing may also be performed. That could include fluorescent penetrant, magnetic particle, radiographic, or other inspections. Final dimensional inspections, alloy test results, and NDT are verified prior to shipment.
Conclusion
The sand-casting process is a versatile and well understood process. Process refinements over time have helped make sand casting the process of choice for applications in many industrial markets.
As with most materials and design decisions, a discussion with a MetalTek expert can help drive the best metals and casting decision. For new designs, conversations early significantly help optimize manufacturability. But even applications that have used metal components the same way for a long time can be evaluated to provide higher performance or find a more cost-effective process like sand casting.
To learn more about this process or to determine if it is a fit for your application, please contact us.