Blog A Look at Using Cores to Create Internal Passageways in Metal Sand Castings
By: Dave Olsen
There are many benefits of using the sand casting process versus traditional manufacturing processes. If you asked multiple metal casting suppliers the main benefit, many would say the cost-effectiveness when internal passageways are required.
How Does A Metal Casting Supplier Produce A Finished Component with These Passageways?
The answer is simple – by using core making in the casting process. While the answer is simple, the process can be highly technical to ensure a quality product. Let’s take a look at the art and science of core making.
What is Core Making in Casting?
A core is an object, typically made from sand or ceramic, that is in the shape of the passageway or void required for the finished component. In a conventional sand casting process, the two mold halves (cope and drag) are matched together, and the resulting cavity creates the exterior geometry and features of the casting. By placing a core inside the cavity, the flow and solidification of metal is redirected around the core, and the internal features and geometry of the casting can be created.
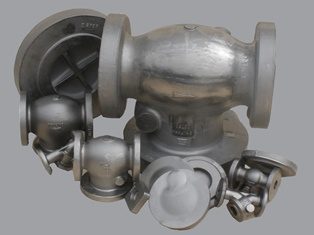
The core must be strong enough to withstand the molten metal’s high temperature with minimal contraction or expansion to avoid dimensional issues of the finished component. However, it must be brittle enough to be able to break apart during the shakeout process to reveal the opening.
The tool to create a core is called a core box. There are various methods to making a core but probably the simplest way is the cold box method. Sand, along with a binding agent, is packed into a core box, the excess removed, and a wooden or metal plate seals in the sand while it is allowed to cure. When ready, the cores are removed and coated with a non-adhesive to provide a smoother service and supply greater heat resistance. If appropriate, the core is placed in an oven to allow the coating to dry and the binding agents in the sand to react.
Keep in mind that using cores will add to the final cost of the casting but working closely with your casting supplier during the design stage and discussing the use of cores can save you money in the long run.
To learn more about the sand casting process, read our blog located here.