Blog Comparing Costs for Investment Casting, Sand Casting, and Centrifugal Casting
When considering the production of complex metal components, it is important to evaluate the costs associated with different metal casting methods. There are several factors that go into “all-in” costs. These factors include tooling and tooling maintenance, material costs and machining.
Below is a comparison of the all-in costs of three popular metal casting processes: investment casting, sand casting, and centrifugal casting. This blog primarily addresses cost factors, but if you are looking for the general advantages and disadvantages of these methods please refer to our blog discussing the basics of metal casting.
Investment Casting | Sand Casting | Centrifugal Casting | |
Upfront Tooling Cost | Medium to High | Medium | Zero to Low |
Tooling Maintenance Cost | Low | Low to Medium | Typically None |
Tooling Storage Fees | Low | Low | Typically None |
Cost To Change Tooling Design | High | Low to Medium | Zero to Low |
Post-Cast Machining Costs | Low | Low to Medium | Medium to High |
Total Labor Costs | Medium to High | Medium | Medium |
Tooling Lead Time | Medium to Long | Short to Medium | Short |
Total Lead Time | Long | Medium | Short |
As-Cast Surface Finish | Excellent | Good | Poor |
Ability to Cast Details / Thin Walls | Excellent | Good | Poor to Fair |
Best Production Run Size | Medium to Long | Low to Medium | All |
Investment Casting Process
Investment casting, also known as lost-wax casting, allows for the creation of intricate and detailed metal parts. Factors that affect investment casting costs are hard tooling, casting size, casting shape, alloy material, quality requirements, dimensional requirements, and quantity.
The largest of the short-term costs associated with investment casting are tooling costs and engineering. The material costs for investment casting include the price of the wax used to create the patterns and the cost of the metal or alloy being cast. Investment casting also requires specialized equipment such as wax injection machines, autoclaves, and furnaces, which contribute to the overall expenses. The ceramic shell used in investment casting can only be used once, which adds to ongoing material expenses.
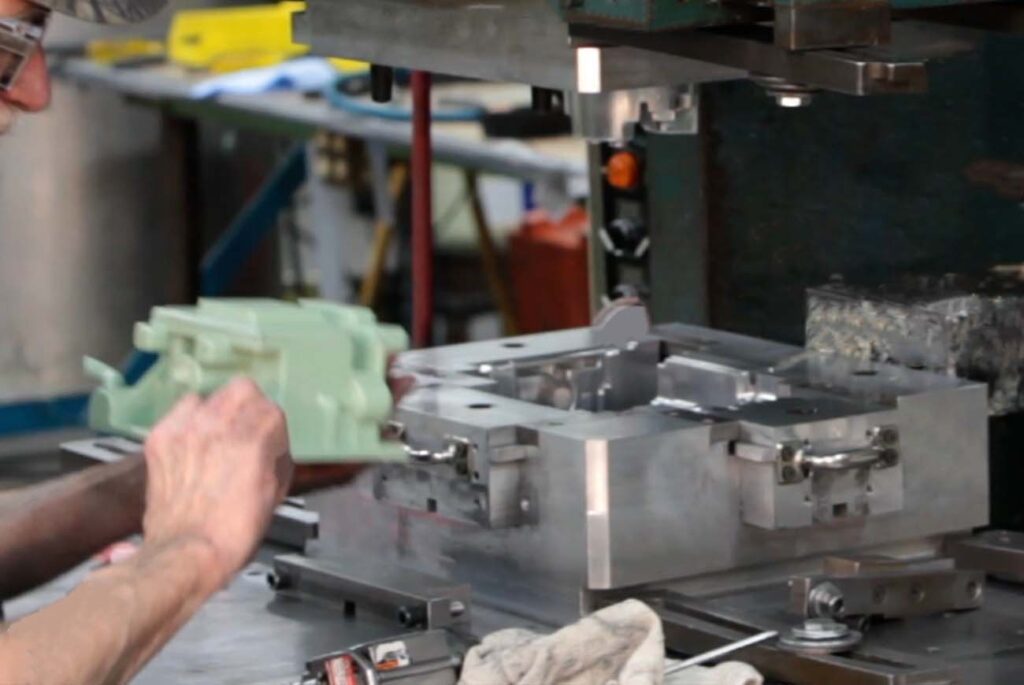
Labor costs associated with investment casting can be higher that other casting methods due to the intricate nature of the process. Skilled professionals are required to create and assemble the wax patterns, invest them in the ceramic shells, and perform necessary post-cast operations such as non-destructive testing (NDT). Changes to tooling design can also affect long-term costs. Of course, tooling for investment casting can be reused, resulting in long-term savings.
Sand Casting Process
Sand casting is the oldest and most widely used metal casting method and involves pouring molten metal into a mold made of compacted sand. This process is highly versatile and suitable for complex components in a range of sizes. Some of the cost factors for sand casting are tooling to create the sand mold, alloys, complexity/scrap risk, order volume, and quality requirements.
Material costs for sand casting include the price of sand, sand binding material, and additives used in mold preparation. Sand casting does not require complex equipment like investment casting and labor costs are typically lower compared to investment casting. Skilled labor is needed to create and prepare the molds, as well as to perform pouring and subsequent processes such as NDT.
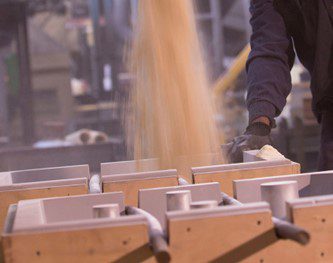
Long-term costs for sand casting can include tooling maintenance and storage fees. Making changes to the tooling/pattern design are an additional cost, but these are not typically as expensive as they are in investment casting.
Centrifugal Casting Process
Centrifugal casting uses centrifugal force to distribute molten metal in a spinning mold or die. This process is known for its ability to produce cylindrical or tubular-shaped components with excellent mechanical properties. Some variables that affect centrifugal casting costs are alloy materials and related processes such as non-destructive testing (NDT) and heat treatment.
Tooling costs are typically limited or non-existent depending on the metal casting manufacturer’s die inventory. MetalTek owns the largest centrifugal die inventory in the world, so it is likely an die already exists for a specific customer application. This keeps the customer’s die costs to a minimum, if not zero.
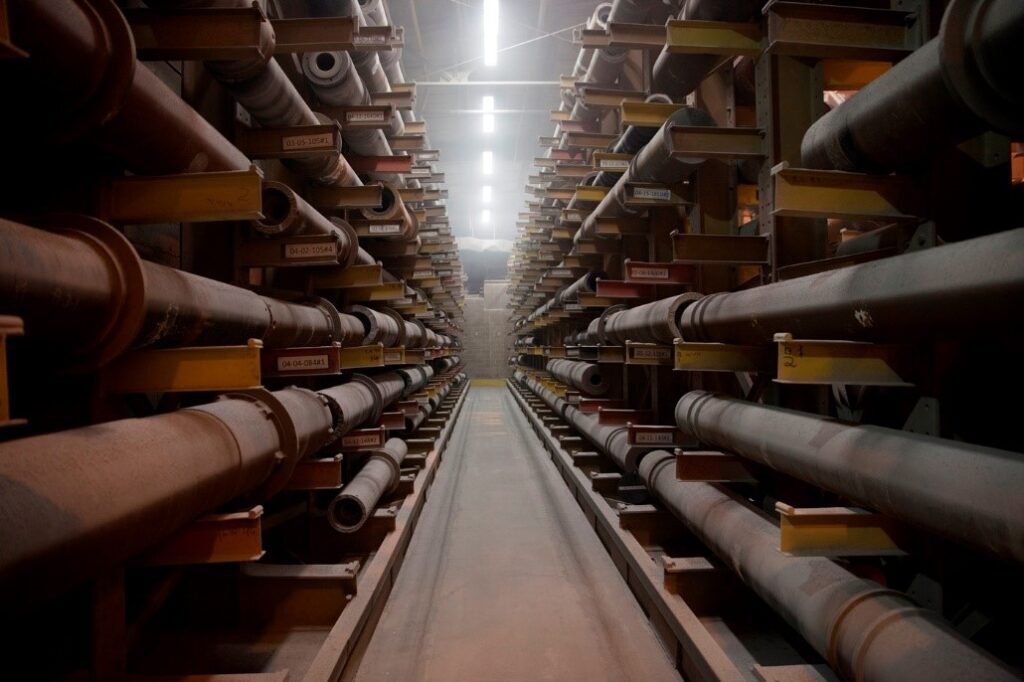
How MetalTek Helps Control Customer Costs
MetalTek’s integrated alloy and manufacturing process expertise is designed to help customers make their products perform better in the world’s most demanding applications. We review the customer’s parts, the application, alloy family/type (if not a specific alloy), and the customer’s needs based on the expected performance of the part.
If the customer does not know what alloy to use, our metallurgists will make recommendations. In some cases, a slight modification to part design can result in significant costs savings through a more efficient manufacturing process. MetalTek’s process engineers are ready to support customers by designing a specific manufacturing process to meet their exact needs.
The choice of metal casting process depends on the specific requirements of the project, including component design, quantity, and desired mechanical properties. By thoroughly evaluating the all-in costs and considering other factors such as production volume and lead time the customer can make informed decisions to optimize their casting processes and get the best cost and quality outcome. Partner with MetalTek and help power, protect, and connect people and businesses worldwide. If you are ready, contact us today.