Blog Copper vs. Brass vs. Bronze – The Difference Between Alloys
By: Scott Derse
Copper vs. Brass vs. Bronze
At MetalTek, one of the elements we work with is copper. The two primary copper alloys are brass and bronze. Brass is made of copper combined with zinc and bronze is an alloy made of copper combined with other elements, historically tin. MetalTek specializes in bronze alloys and does not typically cast purely brass alloys. Simply put, cast brass has too large of a grain structure and lacks the strength-to-ductility ratio required in high-wear applications. MetalTek works a lot with the defense, power transfer, and process equipment industries and cast brass is not a good option. Forged brass is much stronger than brass metal castings. Copper vs. Brass vs. Bronze doesn’t have to be a mystery anymore.
Copper Alloys
Below are two of the primary copper alloys used by MetalTek for various applications.
- C81100 – Copper Alloy: 99.7% Copper minimum, great thermal conductor, corrosion, and oxidation resistance
- C81500 – Chromium Copper: 1% Chromium added, added to increase strength and hardness while maintaining high conductivity
More copper alloys can be found on our copper alloys page.
Advantages of Copper
Basic copper or unalloyed almost 100% copper is highly malleable and corrosion resistant and has distinct advantages in thermal and electrical conductivity. Chrome copper is more than three (3) times stronger than pure copper due to the addition of chromium, but the addition of chromium comes at the cost of lower conductivity. Typically, chrome copper realizes about 80% of the conductivity of pure copper. The various standards of copper conductivity are determined by the International Annealed Copper Standard (IACS).
Copper Applications
Copper’s properties give it malleability, corrosion resistance, and conductivity. These properties make it ideal for “everyday” market applications such as:
- Endings for large motors
- Electrical wiring
- Water piping
- Conductor components
MetalTek produces almost any kind of copper-based material for countless critical applications. Food processing is often ideal for chrome copper alloys due to its high-wear nature. Briquetting rolls are an excellent example. Chrome copper briquetting rolls make uniform shapes that result in your favorite candy.
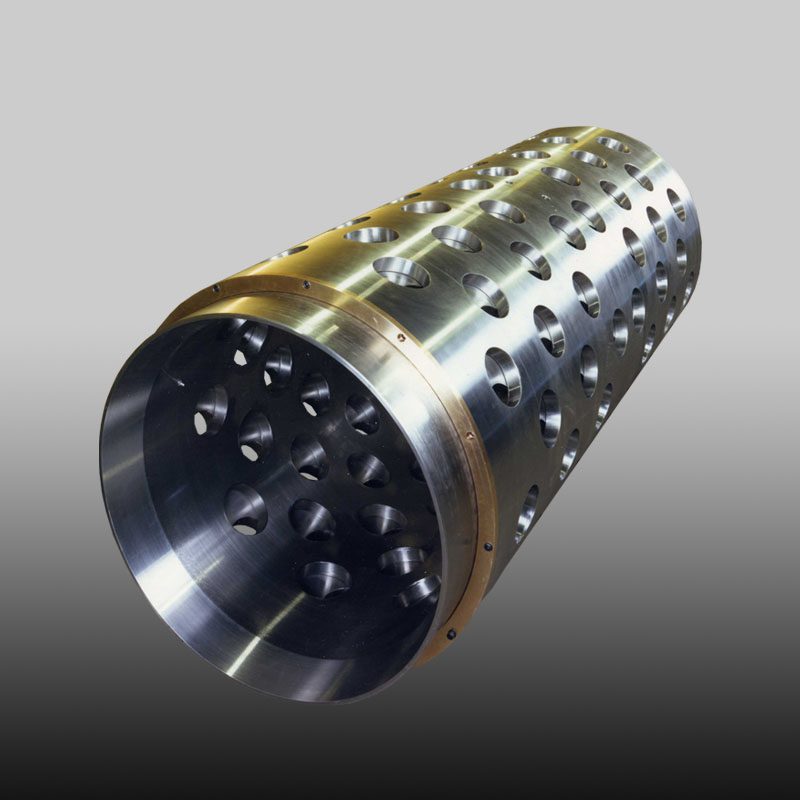
Bronze Alloys
Bronze is a copper-based alloy that features a mix of other metals such as tin, lead, and aluminum. The primary bronze alloys are aluminum bronze, tin bronze, and manganese bronze. Tin bronzes come in leaded and non-leaded versions. Lead is added for lubricity (decreased friction).
MetalTek has a unique added value with higher regulation tolerances for working with lead. We can pour up to 100% lead several days a year.
Below are some of the common bronze alloys at MetalTek.
- C91300 – Tin Bronze: high tensile, yield, and compressive strength
- C95400 – Aluminum Bronze – popular, high yield, and great tensile strength
- C83600 – Manganese Bronze – high strength
- Bearium B-10 – Leaded bronze and proprietary to MetalTek
- MTEK 375 – Aluminum Bronze – unusually high compressive strength, high resistance, and superior non-galling & scratching features
Bronze Applications
Aluminum bronze alloys are noted for their high strength and corrosion resistance. Common applications of aluminum bronze alloys include:
- Naval ship materials
- Components for propellor systems
- Tail cones
- Hub bodies for naval or maritime applications
- Gears for larger parts
- Forming rolls and dies
- Pump and valve components
- Wear rings
Tin bronze alloys have increased wear capabilities, but at a higher metal cost. Common applications include:
- Bearings
- Bushings
- Piston gears
- Steam fittings
- Hydraulic components
- Impellers
High-leaded tin bronze is often ideal for applications where limited friction or abrasion is required. For example:
- Higher speed requirements – holds up better for wear and tear with high friction and/or pressure
- Pump fixtures
- Steam fittings
- Hydraulic components
- Impellers
Manganese bronze alloys are made with high amounts of zinc and are an excellent replacement for typical brass materials. Their high strength makes them ideal for high pressure applications such as:
- Jack nuts
- Bushings
- Flanges
- Forming rolls & dies
- Cams
- Worm gears
- Steel mill nuts
- High strength requirements
- Large valve stems – they have lower corrosion resistance than lead and tin bronze components
MetalTek has extensive experience using these bronze alloys to produce components such as hub bodies and shaft sleeves. Our centrifugally-cast hub bodies help power 100% of guided-missile destroyers (DDGs) in the U.S. Navy and must stand up to the demands of 50,000 horsepower in highly corrosive saltwater environments. Primary alloys used for naval propulsion applications are C96400 70-30 copper nickel (28% to 32% nickel) and C95800 (10% Al, 5% nickel). The addition of nickel improves copper’s strength, durability, and resistance to corrosion.
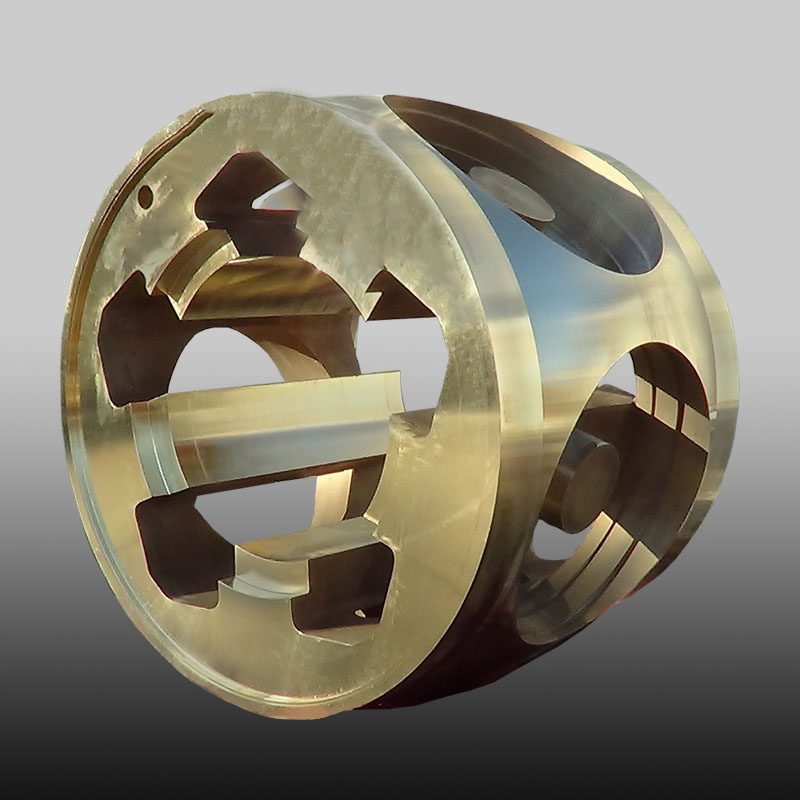
For more information on bronze alloys and the History of Bronze, check out this great blog by Dave Olsen from MetalTek.
Alloy Comparison: Choosing the Right Alloy for Your Application
When choosing between copper, brass, and bronze alloys, understanding the specific demands of your application is crucial. Each alloy offers distinct properties, and selecting the right one can impact the performance, longevity, and cost-effectiveness of your components. Here are some key factors to consider:
- Strength and Durability:
- For applications requiring high strength and corrosion resistance, bronze (especially aluminum bronze and manganese bronze) is often the best choice. It excels in high-pressure environments like naval applications or industrial machinery.
- If malleability and moderate strength are sufficient, brass is ideal for applications like musical instruments, locks, and decorative items, where formability and acoustic properties are important.
- Corrosion Resistance:
- Copper is highly resistant to corrosion, making it ideal for applications exposed to moisture or the elements, such as water pipes and electrical components.
- Bronze, particularly tin and aluminum bronze, is better suited for harsh, corrosive environments, such as those encountered in marine and industrial settings.
- Thermal and Electrical Conductivity:
- If high conductivity is a priority, pure copper or chromium copper alloys provide exceptional thermal and electrical conductivity. This makes copper alloys ideal for electrical wiring and heat exchangers.
- Bronze and brass alloys, while still conductive, may have lower conductivity than pure copper but often provide better strength or resistance to wear in specific applications.
- Wear Resistance:
- For components subjected to friction and wear, bronze alloys (like tin bronze and high-leaded tin bronze) offer superior wear resistance, making them ideal for bearings, bushings, and high-speed components.
- Cost-Effectiveness:
- Brass is often more affordable than bronze and is a good choice for less demanding applications where strength and corrosion resistance are secondary to cost.
- Bronze, especially high-performance alloys, can be more expensive but offers enhanced strength and corrosion resistance, which may justify the higher cost in demanding applications.
Choosing the right alloy requires a careful assessment of your specific needs, from environmental conditions to mechanical performance.
Brass Alloys
Brass is made from a combination of copper and zinc. It is usually made using a forging process and is typically not poured as a metal casting. The properties of brass give it great tensile strength, malleability, and acoustics and is ideal for applications where corrosion resistance and low friction are needed.
Brass Applications
- Decorative items such as hardware finishes
- Locks & hinges
- Musical instruments
- Gears
Why Work With MetalTek?
MetalTek is a market leader in copper and bronze-based alloys for the world’s most demanding applications. We can produce the largest casting sizes in the U.S., including parts up to 180 inches in diameter. Our more than 100 metallurgists and engineers across multiple locations help customers identify the best alloy and metal casting process for their specific material property and application requirements.
Contact us to learn more.
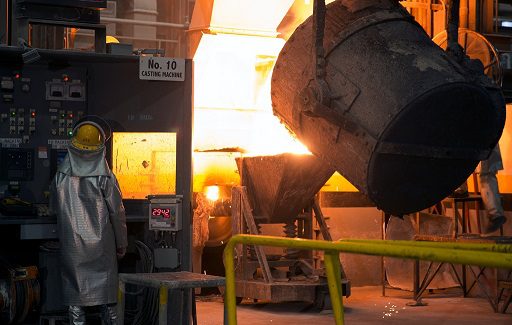
About the Author
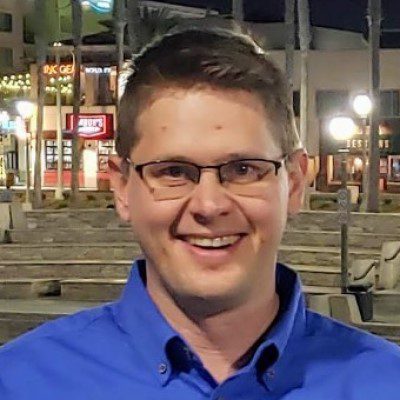
Scott Derse is the primary bronze metallurgist at MetalTek’s Wisconsin Centrifugal Division in Waukesha, WI. He joined MetalTek in 2012 and previously held the roles of Project Engineer, Estimating Engineer, and Chemical Lab Technician. From 2002 to 2010 he served as an Intelligence Analyst in the U.S. Army, attaining the rank of Sergeant. Scott holds a BS in Materials Engineering from the University of Wisconsin-Milwaukee.