Blog Die Casting vs. Investment Casting vs. Sand Casting
By: Dave Olsen
Casting is a manufacturing process of pouring molten metal into a mold to create a desired shape. Once the metal solidifies, the mold is removed, and the part is produced. Three similar casting processes are: die casting, investment casting, and sand casting. Selecting the appropriate casting method for your project is as important as selecting the best metals for each casting type. Below is a description of each casting method, with the advantages and potential disadvantages of each.
Die Casting
What is die casting? Die casting is a casting method that involves injecting molten metal under high pressure into a mold. The mold cavity is typically made of steel and has a shape that matches the desired part or product. These molds are custom made for each project. Die casting is commonly used to create complex, high-precision parts with fine detail and good surface finish.
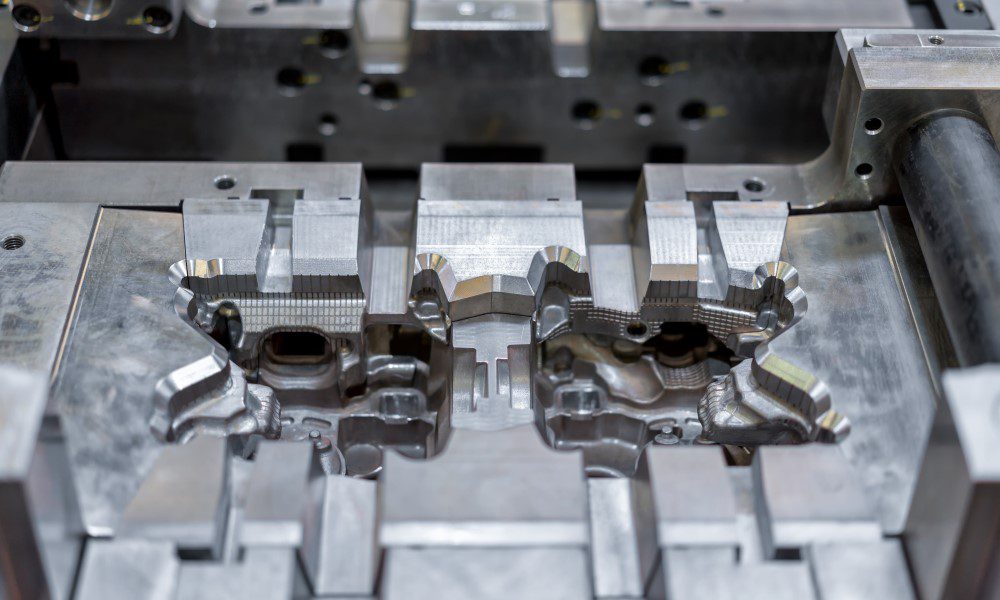
Die Casting Advantages
One of the advantages of die casting is the ability to produce parts with high dimensional accuracy and consistency. Along with the high degree of dimensional accuracy, die casting provides the ability to cast thinner parts. The benefit of thin-walled parts is a lighter-weight part. Parts that require internal cavities and have complex shapes are also a good fit for a die-casting process.
Die Casting Disadvantages
One drawback to die casting is the scale of part sizes. It is typically limited to the production of small to medium-sized parts. Additionally, die casting molds are expensive to manufacture, but the tradeoff is reduced machining and finishing processes. The higher initial cost for the mold can be offset with high-volume production runs. Another drawback is the limit of only using non-ferrous metals such as aluminum, magnesium, or zinc. Ferrous metals typically have higher melting points than non-ferrous metals, which can limit the life of the die.
Investment Casting
The investment casting (or lost wax) process begins with creating a wax pattern of the desired part or product, coating it with a ceramic shell, and then melting the wax out to create a mold cavity. Hot liquid metal is then poured into that mold cavity to create the final metal product. Investment casting is like die casting in that it is ideal for intricate and tighter tolerance parts. Small to medium-sized parts are a good fit for investment casting.
Investment Casting Advantages
Many of the same advantages exist for investment casting as die casting. These include excellent finish, tight tolerances, and reduced machining costs. One of the significant advantages of investment casting is the ability to work with ferrous metals, especially stainless steel and heat-resistant alloys.
Low to medium volume projects are ideal for investment casting. The other significant benefit is the ability to cast larger parts than die casting.
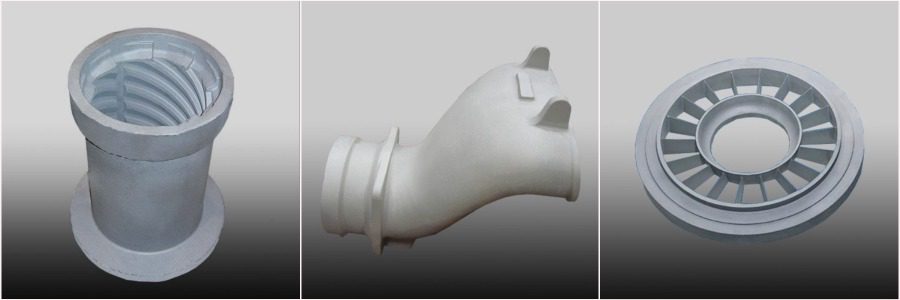
Investment Casting Disadvantages
Investment casting has limitations, like other casting processes. It is typically more expensive than other casting methods, and it is not well-suited for producing extremely large parts. Additionally, investment casting molds can be complex and time-consuming to manufacture. The cycle time for investment casting is longer than other casting methods, which raises the cost. Making one investment casting is slower than a die casting. The primary reason is that the mold for each investment casting needs to be remade each time.
Sand Casting
The sand-casting method forms a mold by packing sand around a pattern of the desired part or product. The pattern is then removed, and molten metal is poured into the cavity to create the final part. Sand casting is a highly versatile casting method that has flexibility when it comes to sizes, shapes, and materials required.
Sand Casting Advantages
The sand-casting method is excellent for larger parts as there is more flexibility and lower cost to produce the molds. Lower production runs are a great fit for sand castings. Sand casting is ideal for parts that do not require tight dimensional tolerances or high degrees of machining.
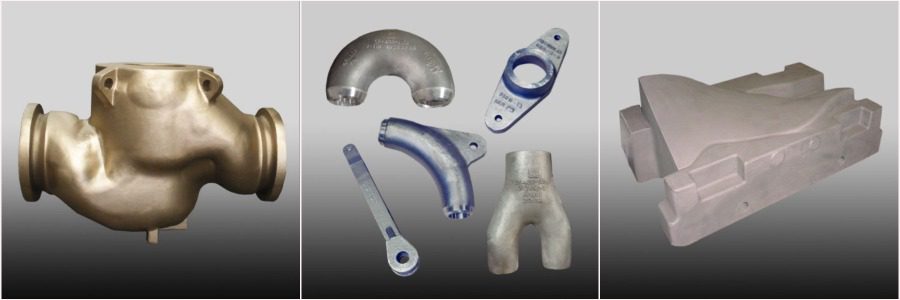
Sand Casting Disadvantages
As mentioned above, sand casting is typically not well-suited for producing parts with high dimensional accuracy and consistency. The rough finishes can require additional machining, but many sand casted parts do not require smooth finishes.
Conclusion: Die Casting vs. Investment Casting vs. Sand Casting
Die casting, investment casting, and sand casting are all casting methods that have unique advantages and disadvantages. Die and investment casting both allow for tight dimensional tolerances and are great for small, intricate parts. Sand casting is better suited for larger parts that do not require complex machining. Scale of production and costs come into play quickly for all three methods. Selecting the correct casting method can be a complex decision at times, but MetalTek experts are here to support customers with investment casting, sand-casting, and centrifugal casting solutions.
Contact us to learn more.