Blog Improving Surface Finish And Cost In Metal Casting
Metal surface finish can play a key role in the metal casting process. Why? Because this affects both how a product works, looks, and its cost. For metal casting, optimizing this process is vital. This article explores the nuances of surface finish in metal casting, offering insights into balancing cost and performance effectively.
The Importance of Surface Finish
Surface finish refers to the texture or smoothness of a surface after it has been manufactured. It is measured in terms of roughness, waviness, and lay. In the metal casting process, achieving the right metal surface is essential for several reasons:
- Performance: A smoother surface reduces friction and wear, extending the life of the component.
- Appearance: For parts that are visible, a good surface finish enhances visual appeal.
- Cost: Achieving the desired surface finish can impact further production costs, influencing the overall budget of a project.
Achieving Optimal Surface Finish
To optimize the surface finish in metal casting, several strategies can be employed:
Metal Casting Process
One of the main factors that play a role in the surface finish is the metal casting process used. Typically, investment casting will provide the best surface finish followed by sand casting. Centrifugal casting provides the roughest surface finish but typically requires additional machining post-casting. While an as-cast surface using the centrifugal casting process is acceptable in some applications, additional machining of the inner diameter (I.D.) is recommended to ensure a quality component.
Mold Design and Preparation
The mold’s surface directly affects the finish of the cast part. A well-prepared mold with a smooth, clean surface will transfer these qualities to the final product.
Additionally, the mold’s design should facilitate even distribution of the molten metal, preventing defects such as porosity or uneven surfaces.
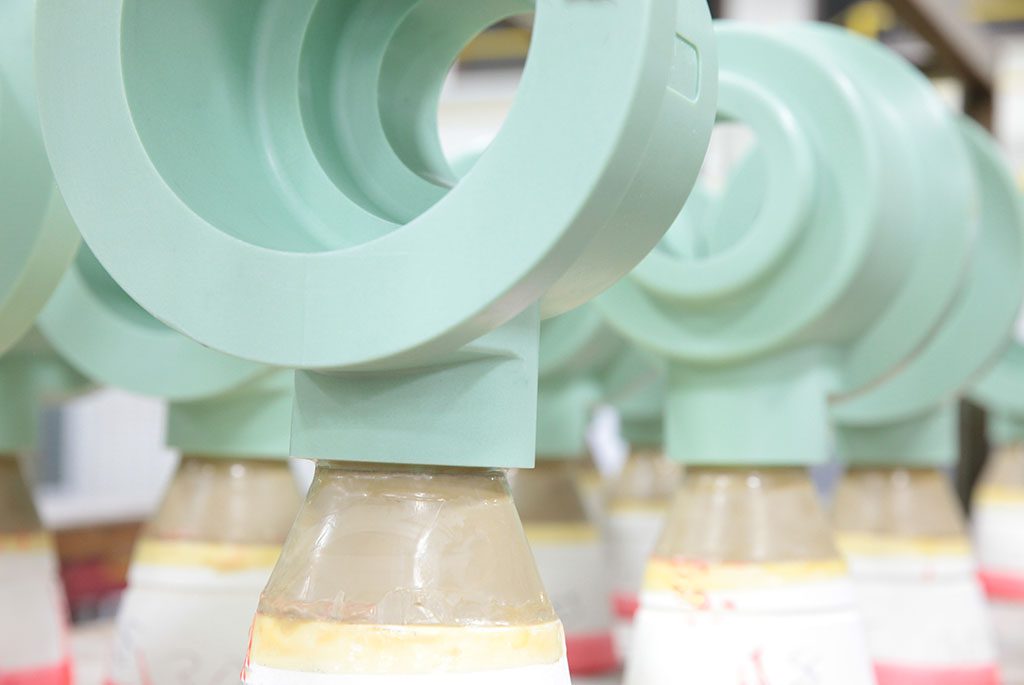
Process Parameters
Adjusting parameters such as pouring temperature, pouring rate, mold temperature, and cooling rate can significantly impact the surface finish.
In regard to centrifugal casting specifically, higher rotation speeds can improve the density and surface smoothness, while precise temperature control ensures that the metal flows evenly and solidifies uniformly.
Post-Casting Treatments
After casting, further treatments can enhance the surface finish. These may include:
- Machining: Removes excess material and smoothens the surface.
- Polishing: Provides a mirror-like finish.
- Coating: Adds protective layers that can also improve the surface’s appearance and durability.
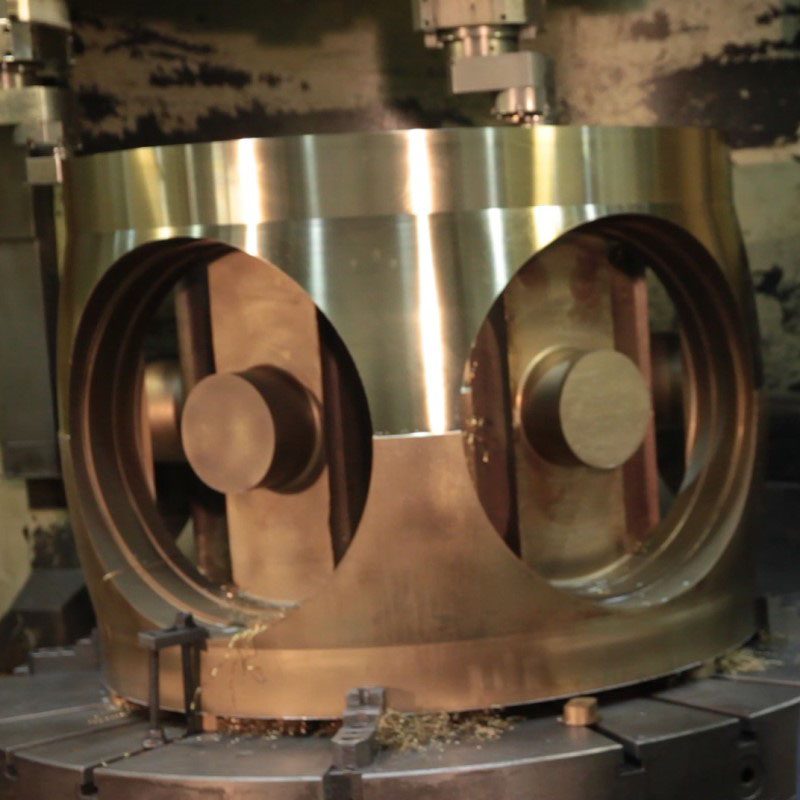
Material Selection
Choosing the right material can aid in optimizing surface finish. Metal alloys react differently when used in the casting process. For example, one metal may flow better than another. In addition, one alloy may solidify in a way that yields a smoother finish than another. Understanding the characteristics of each material helps in making informed decisions that align with project goals.
Balancing Cost and Performance
While a superior surface finish may be desired, it is essential to balance this with cost considerations. Over finishing can lead to unnecessary expenses without significant performance gains. Therefore, the goal is to achieve a finish that meets functional requirements without exceeding budget constraints.
The Role of Quality Control
Effective quality control is vital in ensuring that the desired surface finish is achieved consistently in metal casting. Implementing rigorous inspection protocols throughout the casting process allows manufacturers to identify and address potential issues before they escalate.
Techniques such as surface roughness measurements, visual inspections, and non-destructive testing can help maintain high standards and ensure that finished components meet the required specifications.
Summary
Optimizing the surface finish in metal casting is a delicate balancing act between cost and performance. Choosing the right metal casting process, materials, and post-casting procedures will help achieve desired results. However, one should select a surface finish that meets functional requirements vs. an extremely smooth finish that doesn’t add any value.
Have questions? Working on a project? Contact MetalTek today to see if we can help serve you and your needs.