Blog Material Applications: Corrosion Resistant Alloys
By: Dave Olsen
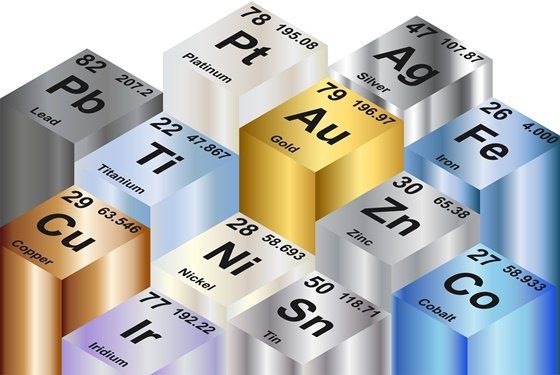
Corrosion is the loss of metal due to a reaction with the environment, and is measured as the percentage of weight loss or as the penetration rate of the corrosion, perhaps measured in inches per year.
Corrosion can develop in the presence of liquids or gases. It may occur at any temperature, although generally the rate of corrosion increases with increasing temperature. Corrosion associated with liquids is often caused by impurities or by trace elements within the liquid. Examples of that would be the presence of chlorine, which encourages formation of hydrochloric acid, or of sulfur, which forms sulfuric acid.
It is important to remember that any alloy, stainless steel or otherwise, can corrode under certain circumstances. The presence of corrosion does not necessarily indicate a faulty product; it may instead indicate an improper application of that product – perhaps using a material that is not the best fit for a given environment, for example.
Corrosion resistant metals, particularly stainless steels, form a very thin chromium oxide layer that protects the inner metal from oxygen. That is important because oxygen is needed with iron to create rust/iron oxide. In general, no oxygen, no rust. The layer is passive – the process is known as passivation – and self-healing; if the surface is scratched, the oxide layer regenerates itself if there is oxygen present.
What Are the Common Types of Corrosion?
There are many types of corrosion and a brief description of some corrosion examples are below. More details about corrosion types are included in another of these newsletters.
- Uniform Corrosion – Corrosion that occurs evenly across all surfaces.
- Pitting Corrosion – Localized attack that creates a pit or cavity.
- Crevice Corrosion – Localized corrosion in crevices or concealed areas.
- Galvanic Corrosion – Localized corrosion where there is an exchange of ions between materials.
- Stress Corrosion Cracking – Where cracks occur in a specific corrosive environment.
- Inter-granular corrosion – Localized corrosion at the metal’s grain boundaries.
- High Temperature corrosion – May take many forms including:
- Oxidation – Natural process where metal is converted to an oxide (actually a more stable state).
- Metal Dusting – A result of a high carbon environment where metal turns to powder.
- Carburization – A severe metal dusting condition which petrochemical applications are designed to resist.
- Sulfidation – A result of naturally occurring sulfur compounds found in crude oil.
- Ash/Salt Deposit Corrosion – When ash or salt are deposited and react with an alloy’s protective oxide layer in certain industrial processes.
- Molten Salt Corrosion – Molten salts remove the oxide layer making the metal susceptible to other types of corrosion.
- Atmospheric corrosion – The most prevalent type of corrosion (rust on iron, e.g.) is a result of the planet’s natural environment of oxygen and water vapor.
- Microbial corrosion – Corrosion caused by the metabolic activity of micro-organisms. It may be aerobic or anaerobic.
What Is The Criteria for Selecting Corrosion-Resistant Alloys?
Metals that are corrosion resistant have the ability to prevent environmental deterioration by chemical or electro-chemical reaction. Desirable characteristics of corrosion-resistant alloys, therefore, include high resistance to overall reactions within the specific environment.
Some of the attractive properties that a metal may feature include:
- Minimized dissolution of the metal in aggressive solutions.
- High resistance to local attack, whether deep penetration in local pitting, networks of local cracks associated with stress corrosion cracking, or intra-granular corrosion.
- Resistance to enhanced corrosion due to the presence of applied or residual stress or the application of fluctuating stress.
- Resistance to enhanced corrosion at the interface under load of two contacting and slipping surfaces.
- Resistance to accelerated local corrosion where mating surfaces of assemblies meet the corrosive environment.
- Resistance to selective dissolution of a more active constituent of an alloy, leaving behind a weak deposit of the other material – for example the dezincification of brass.
- Resistance to the combined action of different corrosion sources.
What Are Some Examples of Corrosion-resistant Alloy Families?
- Stainless Steels: The most common of the corrosion resistant alloys, stainless steel, by definition contains a minimum of 10.5% chromium. The chromium creates a self-healing oxide layer that delivers corrosion resistance. Many other performance and cosmetic features separate stainless steel from other ferrous alloys. Still, care must be taken in selecting the grade as even a trace amount of some elements can impact corrosion resistance, so it is possible to have stainless steel corrosion. This is generally the prime example of a rust-proof metal.
- Copper-based alloys: Other desirable properties combine with corrosion-resistance to make copper-based alloys attractive. Excellent thermal and electrical conductivity, high mechanical properties, and ease of working with the material contribute to its use. While there are some compounds and acids that aggressively attack these materials, they perform well in the air, water, saltwater, and in the presence of many organic and inorganic chemicals.
- Nickel-based: These alloys are of vital importance in industrial uses but only partly because of their excellent corrosion resistant properties. They do resist corrosion in freshwater, in a normal atmosphere, by non-oxidizing acids, and by caustic alkalis. In addition, they also perform well in severe environments that feature both low and high temperature, and high stress. Pure nickel is tough and ductile, but more expensive than other materials
As with dealing with all environmental challenges including temperature extremes or high wear, the demands of harsh corrosive environments suggest that consultation with metallurgical experts will help select the material that provides the needed performance balanced with cost-effectiveness.