Blog Sand Casting Process: Advantages and Limitations
By: Dave Olsen
Benefits of Using Sand Casting
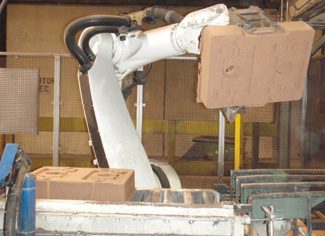
1. Nearly any alloy:
Sand castings can be readily produced in nearly any ferrous or non-ferrous alloy. Some other casting processes will melt and pour super-alloys in a vacuum, but that is not typically done as a sand casting. Some materials cannot be “worked”, and must be produced as a casting.
2. Low tooling cost:
The relatively low cost of tooling makes sand casting a process of choice for lower volume needs. Patterns do wear so the material selected for the pattern (typically wood, plastic, or metal) will depend on the expected usage quantity of the part being produced. Though not necessarily cheaper in the short run, the use of machined (or “patternless”) molds may be a cost-effective option for components with expected lower usage over a longer period of time.
3. Versatile – Size, Weight, Shape:
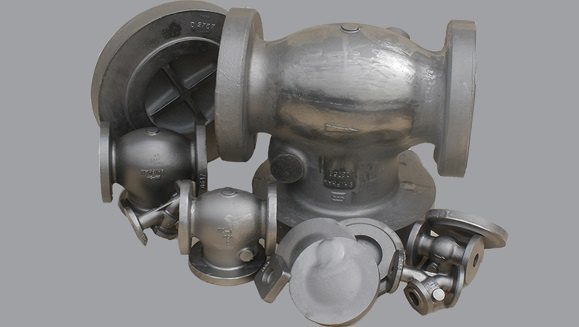
Sand castings can be produced in weights from ounces to 200+ tons. Through the use of cores, internal structures can be cast in place. Shaped parts rely mainly on the imagination of the designer. Most sand castings, however, will need at least some machined surfaces, either because of innate tolerance limits of the process, or the need to mate with other components.
4. Any Quantity:
Because the tooling cost can be minimal, sand casting may be appropriate for a single piece run. Alternatively, there are automotive components that are produced using this process, so it may also be used in high volume applications. Other elements of design and tolerance are often more important than quantity when selecting this as the preferred casting process.
5. Timing:
The casting process itself may be quicker than some others, like investment casting, but it is important to consider the post-casting processes like machining that may be required when computing total lead times.
Concerns with Sand Casting
1. Lower Dimensional Accuracy:
No-bake molding can deliver better dimensional accuracy and repeatability than green sand molding, but this process will, on average, provide less precision than other common casting processes.
2. Pattern Maintenance:
While of lower cost than tooling for other casting processes, there is still an art to pattern creation. Patterns can be bulky so the storage must be managed; this is especially significant if the casting is produced infrequently. Patternless molding can relieve some challenges of pattern storage and maintenance.
3. Surface Finish:
Sand castings tend to deliver a rougher surface finish than other casting processes. That point may be moot if certain surfaces are machined anyway, or if surfaces in the as-cast condition are acceptable.
Below is a comparison of relative surface finishes that can be expected from various casting process:
Casting Process | RMS Range |
Die | 20 – 120 |
Investment | 60 – 200 |
Shell Mold | 120 – 300 |
Centrifugal – Standard tooling | 400 – 500 |
Centrifugal – Permanent Mold | 20 – 300 |
Static – Permanent Mold | 200 – 420 |
Normal Non-Ferrous Sand | 300 – 560 |
Normal Ferrous Green Sand | 560 – 900 |