Blog Sand Casting Process: Featured Solution Examples
By: Dave Olsen
Think of a test that you face in metal component design or application. Here are some examples of products made from sand casting that leveraged its advantages. Maybe you will see a problem you are working to resolve.
High Performance Combined with Light Weight
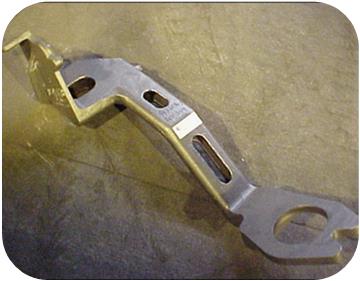
Military hardware transported by air to the place it is needed must be ready to perform, but also must be light enough to be portable. “Box Beam” sand casting sets in radio-graphic quality 17-4PH stainless steel ranging up to 1,000 lbs. and 14’ in length provided the needed strength and weight. The solution was a result of work to select the alloy grade that delivered the needed performance with the right strength to weight ratio and then producing to the standard.
Design and Tooling Capability Saves Development Time
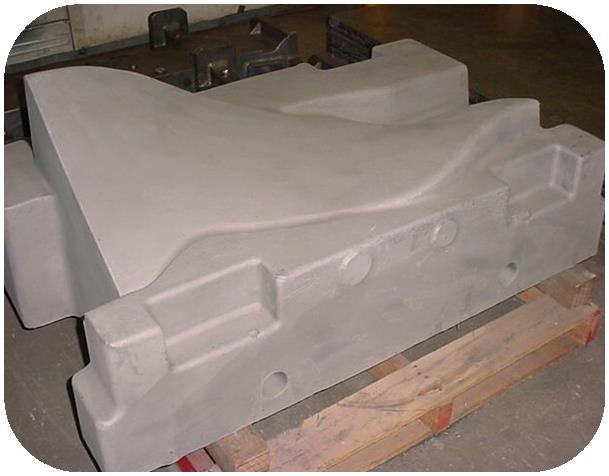
Quick performance, perhaps caused by the need to rapidly develop alternative sources, relies in part on robust design and tooling capabilities. ProE and AutoCAD for in-house design, Magma Soft for solidification simulation takes time and guesswork out of the design process. When combined with the ability to supply patterns in wood, synthetics, metals, and other materials the upfront time to get into production quickly.
Casting As An Alternative to Fabrication In Corrosive Environments

That “fabrication nightmare” is a result of producing parts that need to operate in an environment that demands the corrosion-resistant qualities of nickel-based alloys. These alloys provide superior corrosion resistance, but with their strength comes hardness that makes further processing and machining more difficult than many other alloys. Casting in the needed details, perhaps using a proprietary MetalTek low-turbulence pouring process, turns that fabrication nightmare into a dream.
Working Together to Promote the Customer’s Market Position
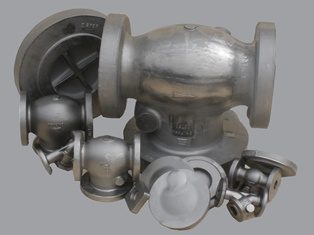
A long-time customer using a different alloy family, wished to expand their product line into different materials to access another key market, but had no supplier willing to develop with them. Partnering with MetalTek in a joint alloy development effort, we collectively worked through process development, product testing, and field trials to devise products that the customer would machine and sell competitively. When our customer is successful, we are successful.
Large Sand Cast Parts That Perform At High Temperatures
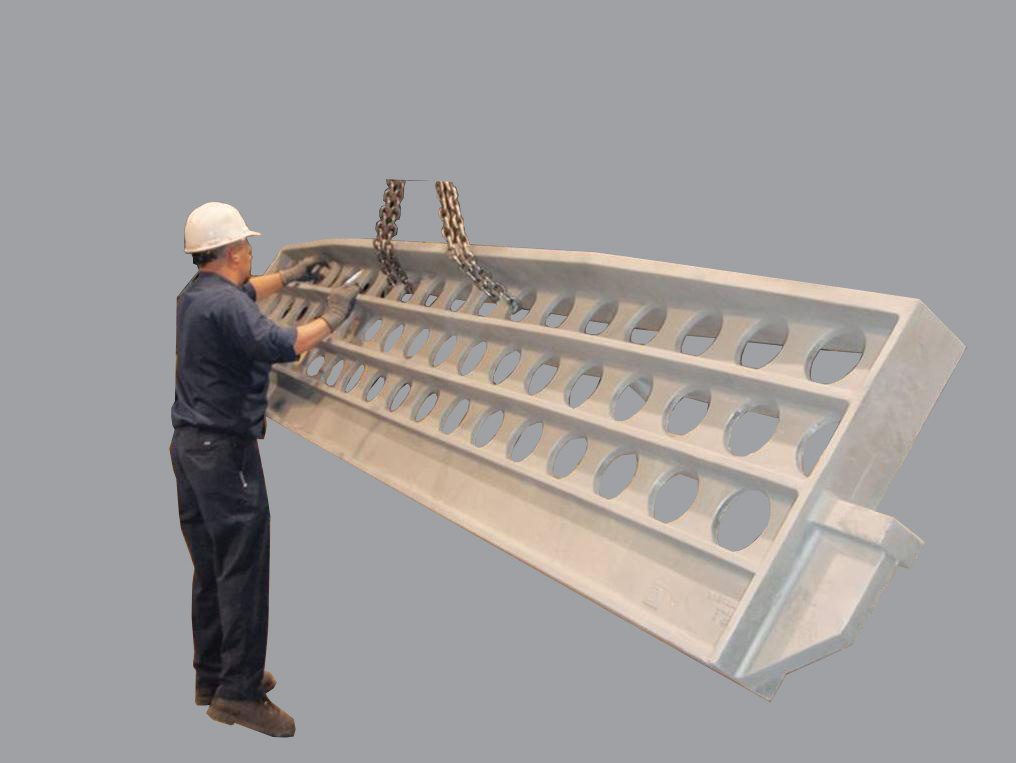
Tube sheets are large cast parts that must operate at high temperature (1,500ºF-2,200ºF) in the convection section of process furnaces. Because of their size and relatively thin walls, tube sheets are prone to stress cracking. Using the proper design, casting process, alloy choice, and balance within the specification, users avoid cracking in those harsh environments. Helping solve their problems is a result of understanding customer-specific operational challenges.
Complete Process Control to Deliver the Right Shape
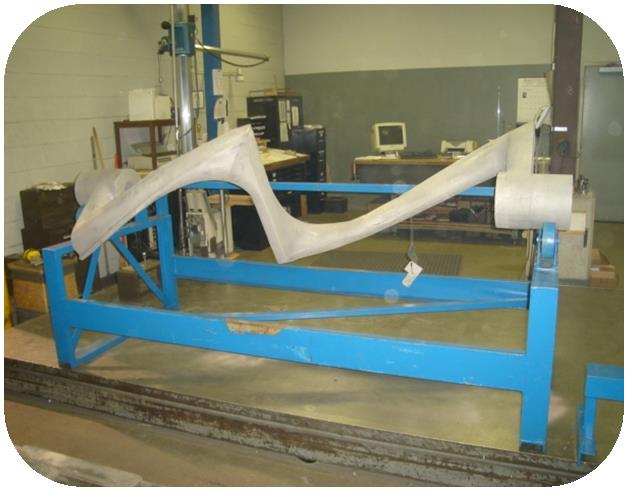
The manufacture of blades used to process highly viscous materials presents particular casting challenges including alloy selection for corrosion resistance, casting, heat treat, and machining of large parts – while retaining their shape. Through the development of materials that did not require water quench to achieve desired corrosion properties, a significant opportunity for product distortion was avoided. Other fixtures simulated the machining envelope to ensure that the cast product could be machined to the desired shape.
Performance In the Most Demanding Environments
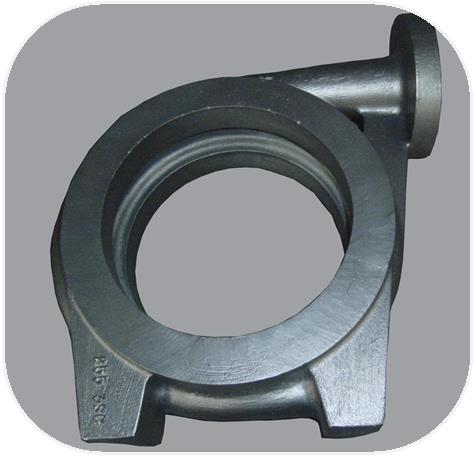
Stainless steel products used in the North Sea oil fields face some of the most demanding environments on the planet. Managing corrosive conditions in areas that are often inaccessible and difficult to service requires a heightened level of quality and reliability. Duplex alloys specified for these applications are strong, resistant to corrosion and stress corrosion cracking, yet more cost-effective than other stainless alloys. As a holder of NORSOK approval for numerous alloys, MetalTek is equipped to provide a wide range of products for those demanding environments.
The versatility of sand casting helps turn metal problems like these into successes. To learn more about this process or to determine if it is a fit for your application, please contact us.