Blog The Beginners Guide to Metal Casting Defects
Metal casting is one of the most widely utilized methods of producing metal parts. Like any process, if not conducted carefully, defects can occur. Defects compromise the integrity and quality of the final metal product and come in a wide variety. Foundry experts can perform various tests to ensure defects are discovered and corrected. However, understanding common casting defects is vital for any metal project.
Common Casting Defects and How to Identify
Porosity
Porosity is a casting defect when gas bubbles become trapped in the solidified metal, creating mini air pockets. This will weaken the final material and impact things such as reduced load-bearing capacity. Cavities discovered on the surface of the metal casting can be classified typically as either pinholes or blowholes. Porosity is often identified through X-rays or visual inspection of the casting’s surface.
Shrinkage
Shrinkage, in the most general sense, is a defect that occurs when the metal contracts during solidification, leading to voids and cavities in the casting. There is improper, dispersed, and axial shrinkage.
Improper shrinkage comes from molten metal added at different rates, resulting in shrinkage. Generally, the metal casting must be redone as this is an original pour issue. Dispersed shrinkage occurs when cavities are created perpendicular to the surface. Axial shrinkage occurs when the center takes longer to solidify than the sides.
Shrinkages can be caused by inadequate gating and riser design. Radiographic testing and visual inspection are commonly used to detect shrinkage defects.
Inclusions
Inclusions refer to foreign particles, such as sand or oxides, that become embedded in the casting during the pouring process. These foreign objects can come from molds, impure materials, ladles, the surrounding environment, or the furnace. The inclusions can weaken areas and reduce the overall quality of the casting. Visual inspection and microscopic analysis are often the methods used for detection.
Coldshuts
Coldshut defects occur when two streams of molten metal fail to fuse entirely during the casting process—resulting in seams or cracks on the surface. Visual inspection and radiographic testing help identify coldshut defects.
Misruns
A misrun is similar to a coldshut. This defect happens when the molten metal fails to fill the mold cavity. This can result in incomplete or misshapen castings. Typically, the edges of the metal casting present with defects. Visual inspection and proper mold design help diagnose and prevent misruns.
Diagnosing Casting Defects
Quality control is crucial from start to finish in the metal casting process to ensure the final product meets the desired specifications. Identifying casting defects can range from simple visual inspections to more technical testing. Metal testing can be broken into four broad categories: mechanical testing, dimensional testing, chemical analysis, and non-destructive testing. Often, multiple tests are utilized for any given project. For a more comprehensive guide to testing standards, please read about MetalTek’s testing and analysis capabilities. Here are four standard methods used to identify metal casting defects.
Visual Inspection
This is as straightforward as it sounds. Experienced inspectors carefully examine the metal castings for irregularities such as cracks, pits, shrinkage, and inclusions. Discoloration or uneven surfaces can also be easily found.
Radiographic Testing
Radiographic testing, including X-rays and gamma rays, is employed to inspect the internal structure of castings. This is a non-destructive test (NDT) typically used for high-specification parts. This method detects hidden defects such as porosity, shrinkage, and internal cracks.
Penetrant inspection
Penetrant inspection is an inexpensive detection method administered on a surface that is oriented in nearly any direction. Penetrant Inspection may take the form of Fluorescent Penetrant Inspection (FPI) or visible Liquid Penetrant Inspection (LPI).
One limitation of penetrant inspection is that the defect must be open to the surface. Penetrant materials are chosen and developed to match the nature of the part surface and desired detectability of flaws.
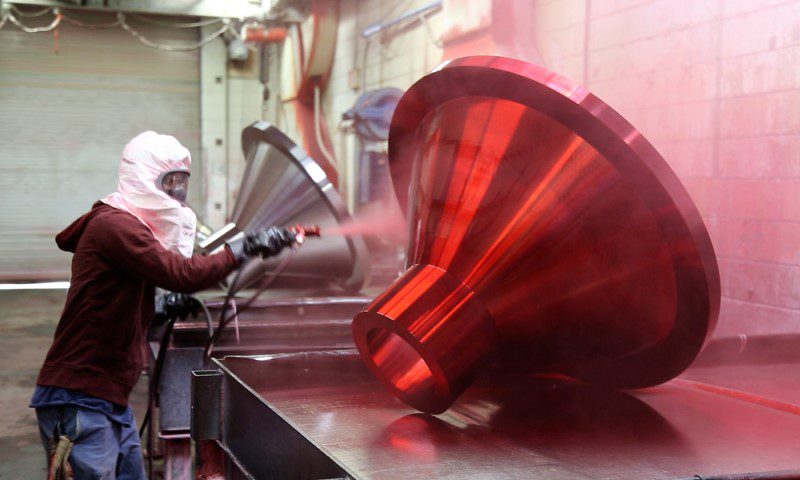
Hardness Testing
Passing a hardness test is a widespread requirement for any metal casting project. Three different hardness tests can be employed. The Brinell Hardness Test, The Rockwell Hardness Test, and the Vickers Hardness Test. Each can be implemented depending on time, accuracy, and cost requirements. This is a standard mechanical test.
MetalTeks’ team of engineers and inspectors comes with years of expertise to ensure quality casts are conducted every time. For a complete guide to the metal casting testing process, check out our thorough analysis blog about Metal Casting Inspection Methods. There is never one test that fits every project, and often multiple tests are used. Casting defects come up regardless of how good the process is, but our team understands them and is ready to respond. Speak with an expert at MetalTek today about your metal casting needs.