Blog Tooling And Forming Dies: Tips For Selecting The Best Alloy For Your Application
By: Dave Olsen
You have designed your tooling or forming die based on the finished part you need, and you know how you will manufacture the tool or die. Perhaps you plan on utilizing MetalTek’s sand or centrifugal casting processes. However, you need to determine the best alloy for your tooling or forming die. Since every application is different, there is no magical “one size fits all” alloy for tooling but this article will provide tips for choosing the best alloy based on your application, requirements, and potential challenges you currently face.
If, after reading this article, you need additional assistance, MetalTek is here to help and we would love to hear from you.
Factors in selecting the best alloy for your tooling or forming dies
When selecting an alloy, there are two primary factors to consider – physical and mechanical properties.
- Mechanical properties are how the metal performs when different forces are applied to them. That includes things like strength, ductility, wear resistance, etc.
- Physical properties are measurable. Those are things like density, melting point, conductivity, coefficient of expansion, etc.
Typically, an alloy’s mechanical properties are used for selection but there are physical properties to keep in mind as well. So, let’s dive a little deeper and look at which specific properties should be considered when selecting the right alloy for your tooling application.
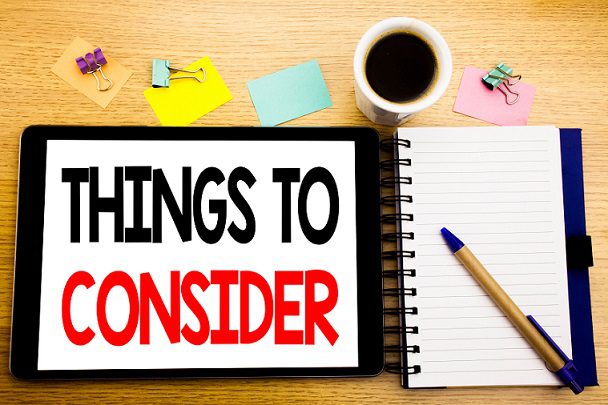
Yield Strength
Yield Strength describes the point after which the material under load will no longer return to its original position or shape after the stress no longer exists. Deformation moves from elastic to plastic. Design calculations include the Yield Point to understand the limits of dimensional integrity under load. Yield strength is measured in Newtons per square millimeter (Mega Pascals or MPa) or pounds per square inch (PSI).
Permanent deformation in tooling is typically unacceptable because it leads to inconsistent parts and premature replacement. To help prevent this from happening, make sure you select an alloy with a yield strength higher than the forces put on the tooling.
Fatigue Strength
Fatigue can lead to fracture under repeated or fluctuating stresses (for example loading or unloading) that have a maximum value less than the tensile strength of the material. Higher stresses will accelerate the time to failure, and vice versa, so there is a relationship between the stress and cycles to failure.
Fatigue limit, then, refers to the maximum stress the metal can withstand (the variable) in a given number of cycles. Conversely, the fatigue life measure holds the load fixed and measures how many cycles the material can withstand before failure. Fatigue strength is an important consideration when designing components subjected to repetitive load conditions.
Does your tool need to make 5 parts before being replaced or does it need to make 5,000? Depending on how many parts your tooling needs to produce (cycles), this is a critical factor in selecting the right alloy.
Hardness
Hardness is defined as a material’s ability to resist permanent indentation (that is plastic deformation). Typically, the harder the material, the better it resists wear or deformation. The term hardness, thus, also refers to local surface stiffness of a material or its resistance to scratching, abrasion, or cutting. Hardness is measured by employing such methods as Brinell, Rockwell, and Vickers, which measure the depth and area of a depression by a harder material, including a steel ball, diamond, or other indenter.
Coefficient Of Thermal Expansion
Coefficient of thermal expansion measures how much a material expands when heated. Since many forming processes involve elevated temperatures, along with heat/cool cycles, alloys with low coefficients of thermal expansion will help maintain dimensional accuracy.
Shear Strength
Shear occurs when directional forces cause the internal structure of the metal to slide against itself, at the granular level. Shear strength should be considered in applications where the direction as well as the magnitude of the stress is important because of extensive shear or torsion loads.
What Are Common Metal Alloys Used For Tooling Applications?
While some tooling is made of non-ferrous metal or even a non-metallic material altogether, ferrous alloys are the most common. More specifically, popular groups of alloys (alloy families) are specialty alloys, stainless steels, tool steels, and carbon steels.
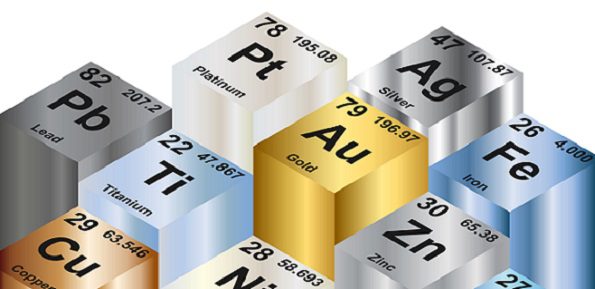
Specialty & Nickel Based Alloys
Heat Resistant Stainless Steel
Heat-resistant alloys are those capable of being used at temperatures above 1200ºF / 670ºC under load in particular gas environments and are indicated by acceptable levels of stress rupture and creep strengths that correspond to the required time of service. Main groups of heat-resistant alloys are high chrome nickel austenitic alloys a.k.a. heat resistant stainless, nickel-based alloys, and cobalt chrome nickel-based alloys. Common heat resistant stainless steels used for tooling applications are: MTEK 20-25, MTEK 20-25MA, MTEK 25-12.
MTEK 625 (Inconel 625®)
MTEK 625 (Inconel 625®) is designed for some of the toughest applications in manufacturing. It works extremely well in high heat applications and doesn’t lose much tensile strength at elevated temperatures like other steels. As a result, it resists deformation at hot-working temperatures. Inconel 625® is not only stronger than stainless steel at elevated temperatures, but it also offers better resistance to corrosion, oxidation, and scaling. Because of its properties, it works well in extreme pressure and heat environments as well as being corrosion resistant.
MTEK Invar (K93600, FeNi36)
MTEK Invar (K93600, FeNi36) is an alloy with 36% nickel and is strong, ductile, and fairly corrosion resistant. What makes Invar a great alloy is that the coefficient of thermal expansion is nearly zero. As a result, it offers dimensional stability across a range of temperatures – cryogenic temperatures to 500°F.
Invar’s coefficient of thermal expansion properties makes it a good candidate for the manufacturing of precision instrumentation and equipment like tooling for aerospace components, electronic devices, and lasers.
MTEK Alloy X
MTEK X is a nickel-based alloy with outstanding high temperature strength at 1500°F and oxidation resistance up to 2200°F. It’s also resistant to stress-corrosion cracking in high temperature applications and has good ductility when exposed to high temperatures for extended periods of time. While nearly half of the alloy is made from nickel, it contains roughly 22% chromium and 18% iron.
Stainless Steels
A common type of alloy used is stainless steel because of its temperature and corrosion resistant properties. Stainless steels owe their ability to resist corrosion primarily to the presence of a passive film on their surface.
Chromium is chiefly responsible for the formation of the passive film. Iron ceases to rust at approximately 12% chromium content and resistance to oxidizing corrosives increases rapidly with chromium content up to approximately 20%. Beyond that level, resistance is increased at a more gradual and declining rate. Consequently, few stainless alloys contain more than 27% chromium.
Within the stainless-steel family, there are four main categories-austenitic, duplex, precipitation hardening, and martensitic. Common stainless steels used for tooling applications are: MTEK 304, MTEK 304L, MTEK 309, and MTEK 310.
Tool Steels
Tool steel alloys are high carbon chrome steels containing various amounts of molybdenum, cobalt, vanadium, and other elements. Some tool steels are designed to handle repeated loads and impacts at ambient temperature with exceptional wear resistance. Other tool steel alloys will exhibit stability at elevated temperatures and repeated loads.
Tool steels are typically provided in an annealed condition which softens the very hard material so that it may be machined or formed for use. After machining, the material is heat treated again to increase toughness and strength.
There are several classes of tools steels available which can be selected based on the specific environment, particularly allowing for temperature. Among those are Cold-work, Hot-work, and High-speed.
- Cold-work tool steels feature strength, impact toughness and wear resistance. They are typically used in temperatures that do not exceed 400°F / 200°C.
- Hot-work tool steels combine the strength, impact toughness and wear resistance with the ability to perform at higher temperature.
- High-speed tool steels deliver strength, impact toughness, and wear resistance and can retain those properties in environments of 1000°F / 540°C.
- Common tool steel grades include: MTEK A2, MTEK A6, MTEK D2, MTEK D5, and MTEK H13.
Carbon Steels
Carbon steels are primarily made from iron and carbon and are the cheapest alloy for tool applications. As a result, it’s one of the most common alloys used for tools. Carbon steels are categorized by their amount of carbon-low, medium, and high.
- Low-carbon steels are the softest, so they are easily machined and welded but don’t offer great strength or wear resistance compared to other carbon steels. As the carbon level increases, the strength increases as well.
- Medium-carbon steels offer higher strength and toughness but are harder to machine and weld.
- High-carbon steels should be in applications that wear resistance important. However, are going to be more difficult to machine and weld compared to low or medium-carbon steels.
When selecting a specific carbon steel alloy, it’s critical to find the right balance between performance and labor costs for machining and/or welding.
MetalTek’s Top Three Picks To Consider
There is no “one size fits all” when it comes to picking the best alloy for every tooling application. However, if you are looking to make your products better or solve a current problem you are having, the below are MetalTek’s top three alloys to consider. See charts for typical chemistry and mechanical property ranges.
To learn more about what alloy might be the best fit for your application, please contact us.
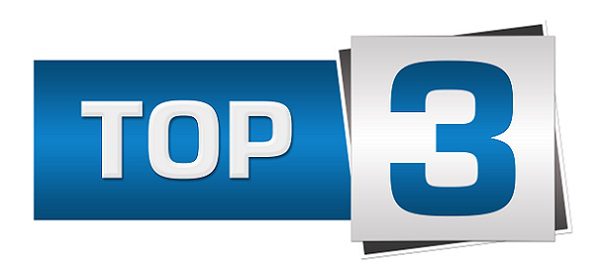
Disclaimer: The information in this publication is for informational purposes and does not replace good engineering practices. MetalTek International does not give any warranty or assumes any legal liability for its accuracy or completeness. In addition, the company makes no warranty of results obtained for any specific use of the information given in this publication.
#1) MTEK Invar: Great strength and toughness and a superior coefficient of thermal expansion.
#2) MTEK 625: Can withstand some of the toughest applications in manufacturing. It works extremely well in high heat applications and doesn’t lose much tensile strength at elevated temperatures like other steels.
#3) MTEK 20-25: All around good alloy for strength and toughness over a range of temperatures. If you are looking for something better than a typical stainless steel like 309 or 310, this might be a good place to start.
METALTEK GRADE | CAST UNS | CAST GRADE | C | Cr | Fe | Ni | Mn | Si | OTHER |
MTEK INVAR | K93600 | Invar 36® | 0.10 MAX | 0.25 MAX | BAL | 35-36 | 0.50 MAX | 0.35 MAX | |
MTEK 625 | N26625 | CW6MC | 0.06 | 20-23 | 5.0 MAX | BAL | 1.00 | 1.00 | Mo 8-10; Nb 3.15-4.50 |
MTEK 20-25 | J94213 | HN | 0.20-0.50 | 19-23 | 23-27 | 2.00 | 2.00 |
METALTEK GRADE | CAST UNS | CAST GRADE | TENSILE ksi / [Mpa] | YIELD ksi / [Mpa] | ELONGATION % | BRINELL TYPICAL |
MTEK INVAR | K93600 | Invar 36® | 48 / [331] | 31 / [213] | 42 | 125 |
MTEK 625 | N26625 | CW6MC | 70 / [485] | 40 / [275] | 25 | 163 |
MTEK 20-25 | J94213 | HN | 63 / [435] | 38 / [262] | 8 | 160 |
A Quick Note About Material Costs
While selecting the best alloy based on the application should be the top priority, other factors to consider is cost, both upfront and long term.
If a specific alloy causes the total cost of the forming die to be twice as much, can you manufacture at least twice as many parts? If paying twice as much yields four or five times as many parts versus using a standard type of alloy, higher upfront tooling costs may be the best long-term decision.
On several occasions, MetalTek has worked with a customer to fully understand their application to recommend the best alloy for the job to make their products better and last longer. In turn, saving money in the long run.
Disclaimer: The information in this publication is for informational purposes and does not replace good engineering practices. MetalTek International does not give any warranty or assumes any legal liability for its accuracy or completeness. In addition, the company makes no warranty of results obtained for any specific use of the information given in this publication.