Blog Tooling for Investment Casting: What Is The Process and How Does It Work?
Investment casting (also known as lost-wax casting) is a common manufacturing process used to create metal parts with fine detail and tight tolerances. The investment casting method involves the creation of a tool, typically made from a high-grade aluminum alloy, that serves as a mold for wax. Hot wax or plastic is poured into the tool pattern. Once hardened the wax is removed and then coated with ceramic and stucco material. This ceramic shell is heated until the wax or plastic pattern melts away, leaving behind a hollow ceramic shell called the mold. Molten metal is poured into the mold, creating a final metal part that is an exact replica of the original wax or plastic pattern.
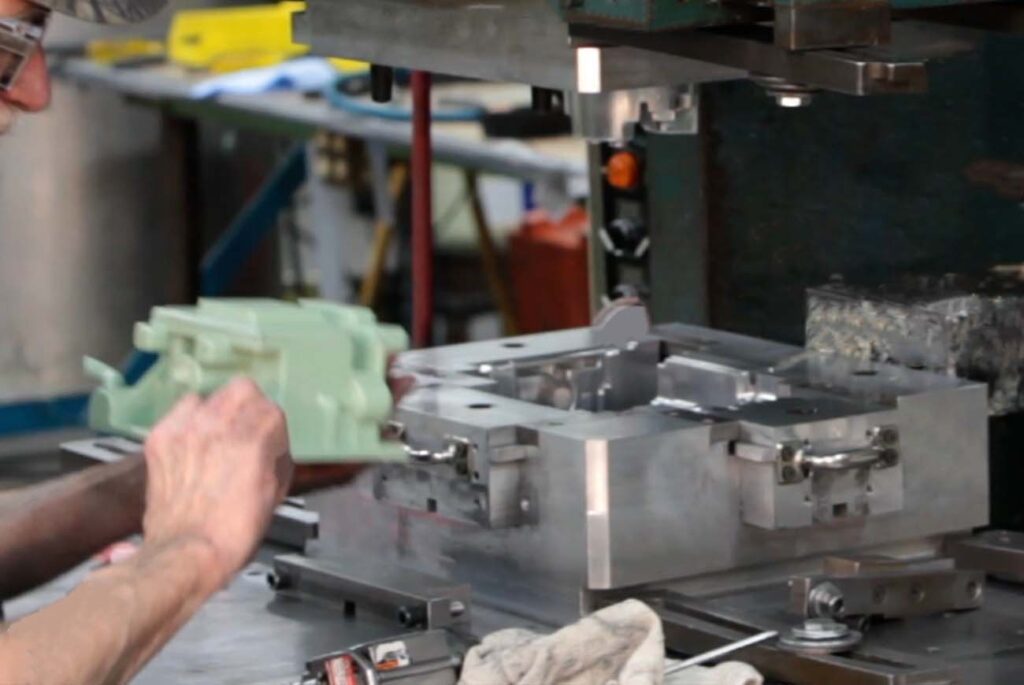
Investment casting relies heavily on precise tooling and equipment to ensure that the final metal part meets the specifications. Tools for investment casting are typically created through a multi-step process that involves several stages of design, fabrication, and testing. Customers of MetalTek are involved in designing the tooling process to ensure it meets all requirements.
Tooling Design
The first step is to create a design for the tool. This is usually done using computer-aided design (CAD) software, which allows engineers to create a 3D model of the tool. The tooling design process can be expensive and is often priced into the quote as a separate item. Ensuring the design is accurate and meets all specifications is critical, as the tool is reusable for potentially thousands of times. MetalTek works closely with every customers throughout this design process.
Creating The Wax Injection Tooling
Once the design is complete, the tool is fabricated using a variety of techniques, depending on the complexity of the tool and the materials being used. Some common fabrication techniques include CNC machining, laser cutting, and 3D printing.
The wax injection tool consists of a metal mold or die that is designed to hold the wax or plastic injection. The tool is typically made from aluminum or steel and is created using CNC machining or other precision manufacturing techniques. The wax injection tool works by injecting liquid wax or plastic into the mold under high pressure. The wax is then cooled and what remains is an exact copy of the final metal part. The wax or plastic pattern is then removed from the mold and heads to the next steps in the investment casting process.
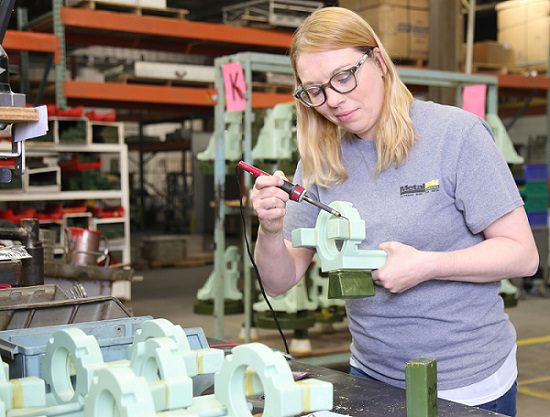
The designs in the tooling process can be highly intricate. There can be no cavities, single cavities, or even multiple cavities. The dimensional tolerances can be extremely tight. This is an added benefit to this process unlike sand casting with lower dimensional tolerances.
Testing and Production
After the tool has been created, it is tested to ensure that it will perform as expected. This involves testing for dimensional accuracy, durability, and other factors that could affect the quality of the casting. If issues are identified during testing, the tool is adjusted before any production begins. The time spent refining and testing can ultimately remove customer cost from the process. Even small variations in the tool can have a significant impact on the quality of the final casting. Once tested and approved by the customer, production can begin, and the investment casting process moves forward with the tooling part.
Considerations For Tooling Design
When pouring or injecting hot wax into the tool, engineers must consider expected shrinkage. They must calculate based on the size and metal type, because as the metal cools in the final pour it will shrink. Additionally, the tooling is often designed to be removable or disassembled easily to remove the wax injection safely and accurately.
Tooling is often considered the ownership of the customer after payments are settled, but storage of the tool is important for future uses. The tooling design is also considered proprietary information as each design is unique.
Tooling For Investment Casting: Conclusions
Overall, the tooling used in investment casting is critical to the success of the process. It determines the quality and accuracy of the final part, and any defects or imperfections in the tooling can result in sizeable defects in the final part. On that note, it is important to work with experienced and skilled professionals who have the expertise to design and manufacture high-quality tooling for investment casting. Contact us to learn more.