Blog What Are Ferrous Alloys?
By: Dave Olsen
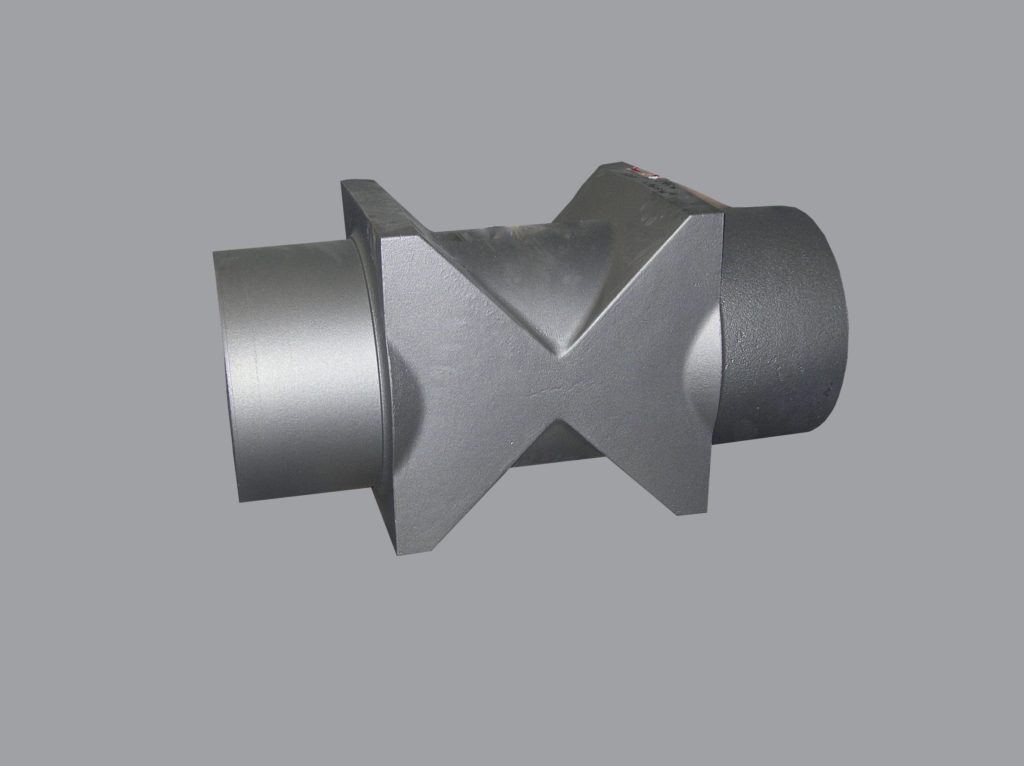
Ferrous alloys (ferro alloys) or metals are metals that consist mostly of iron (Fe). Steel is an iron-based alloy containing typically less than 1% carbon, where iron frequently contains 2% or more carbon. Iron and steel are widely available, strong, cheap, and can be shaped by casting. Ferrous alloy properties can be improved by heat treating and, in the case of steels, by working (i.e. rolling or forging).
Is stainless steel ferrous?
Yes. Stainless steels were developed to resist corrosion and generally contain 12% or more chromium and may contain nickel in any amount up to or even exceeding the chromium content based upon the mechanical properties desired and application.
There are several types of stainless steel. When considering these alloys for use in a corrosive environment, the most widely used method for initial selection is to compare PREn ratings (pitting resistance equivalent number) across materials. This is calculated using the weight % of key alloying elements present in any particular grade of stainless steel. The formula is:
PREn = % Cr + (3.3 x % Mo) + (16 x % N)
Obviously, alloys containing the highest amounts of chromium, molybdenum, and nitrogen are considered to possess better resistance to pitting corrosion. This may be accompanied by a corresponding increase in tensile and yield strengths.
For a quick guide to what is metals are ferrous, here is a Ferrous Metals List:
- Steel
- Cast Iron
- Titanium
- Mild Steel
- Stainless Steel
- Wrought Iron
Ferritic Stainless Steels
Stainless steels owe their ability to resist corrosion primarily to the presence of a passive film on their surface. Chromium is chiefly responsible for the formation of this passive film. Iron ceases to rust at approximately 12% chromium content. Resistance to oxidizing corrosives increases rapidly with chromium content up to about 20%. Beyond that level, though, resistance increases at a more gradual and declining rate. Consequently, very few stainless alloys contain more than 27% chromium. These alloys are composed principally of chromium and iron, with low carbon content. Alloys are often categorized by their crystal structure, which is impacted by chemistry and processing, including heat treating. Ferritic stainless steels have a crystal structure that is chiefly ferrite.
Martensitic Stainless Steels
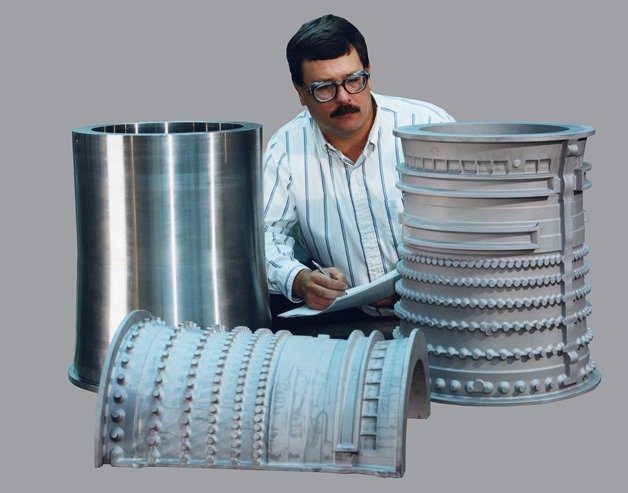
The addition of sufficient carbon to alloys of chromium and iron results in alloys that can be hardened and tempered. Corrosion resistance is reduced somewhat by the carbon level, but the reduction is minimized when these alloys are fully hardened and tempered. Consequently, the higher carbon alloys (over 0.15% C) are normally used only in the fully hardened and tempered condition. Their structure upon rapid cooling from temperatures above 1600°F / 870°C is chiefly martensitic.
Common martensitic grades include: MTEK 410, MTEK 416, MTEK 420, MTEK 431, and MTEK 440.
Austenitic Stainless Steels
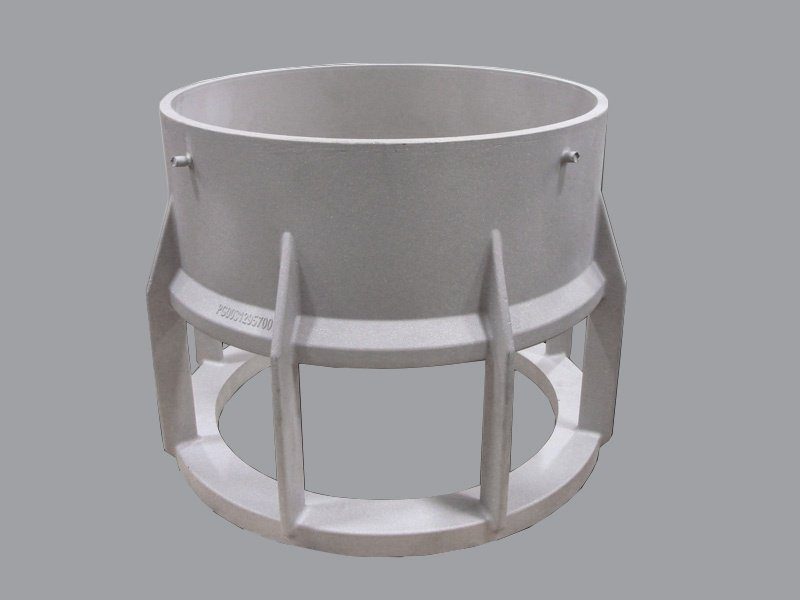
Of all elements added to the basic alloy of chromium and iron, nickel is the most important. It not only improves corrosion resistance but also changes the alloy’s structure and mechanical properties. As nickel is added in increasing amounts to a ferritic iron/chromium alloy, the structure of the alloy changes from ferrite, through mixed ferrite and austenite, to essentially all austenite. Most “18-8 grades” (a common description of 304 stainless that is made up of roughly 18% chromium and 8% nickel) are made with controlled amounts of ferrite for improved welding characteristics and higher strength. The change in structure is accompanied by a marked increase in ductility and toughness. Stainless alloys, predominantly austenitic in structure, make up a family of stainless steels that are by far the most widely used of all types.
Super Austenitic Stainless Steels
Under certain aggressive conditions, the general grades of austenitic stainless steel are more susceptible to pitting, crevice corrosion and stress corrosion cracking. This has led to development and additions to the austenite family, referred to as super austenitic stainless steel.
The use of super austenite is rapidly growing due to changing conditions in today’s process industries. A “fit it and forget it” approach is being adopted to employ alloys which do not require constant, regular replacement in conditions such as deep sea water and high-temperature closed circuit process plants.
Super austenitic stainless steels contain high levels of chromium and nickel together with significant additions of molybdenum and nitrogen. The result is a series of austenitics. They are up to 30% stronger than conventional 300 series stainless and offer superior resistance to pitting, crevice corrosion, and stress corrosion cracking. An austenitic stainless steel is considered super austenitic when its PREn exceeds 40.
Common super austenitic grades include: MTEK 20, MTEK 20M, MTEK 6XN, and 254SMO®.
Duplex Stainless Steels
Duplex stainless steels are alloys with structures generally regarded as being approximately equal parts of austenite and ferrite, with a 60/40, 40/60-phase distribution being the envelope widely considered as acceptable.
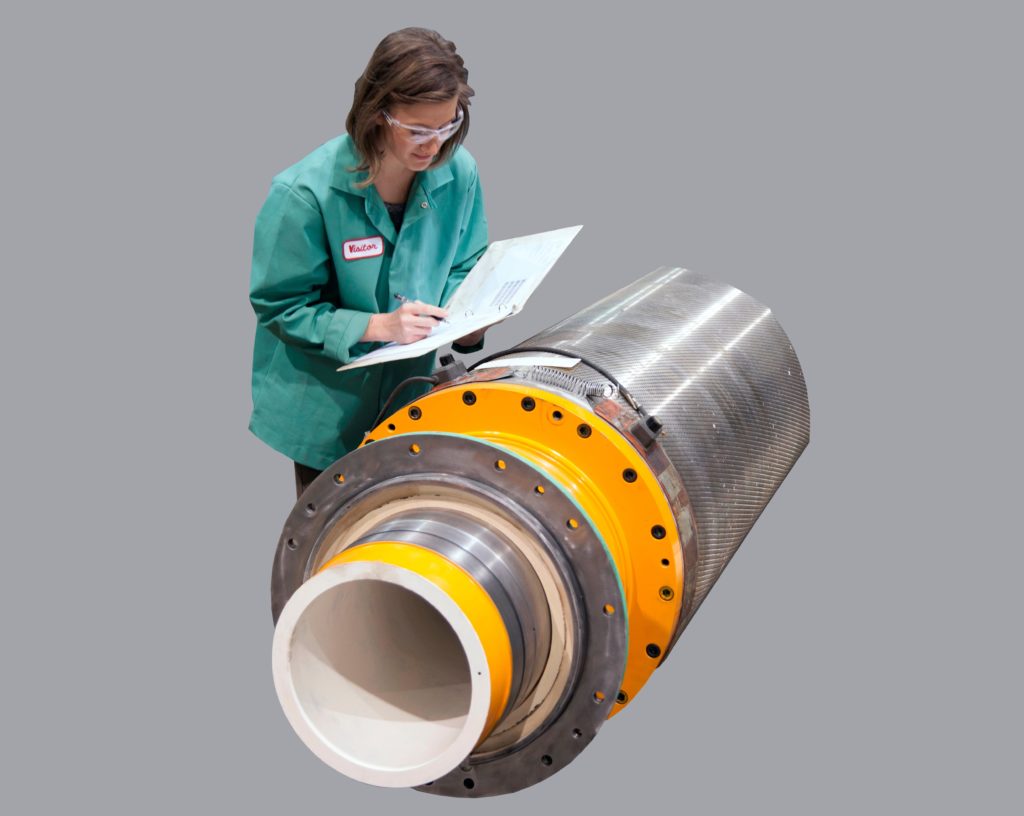
The combination of austenite/ferrite produces alloys with twice the strength of conventional austenitic stainless steels.
Duplex stainless steels are virtually immune to stress corrosion cracking (the Achilles’ heel of common austenitic stainless steels) and are highly resistant to pitting and crevice corrosion. Possessing these characteristics, it is not surprising to find the majority of (but by no means all) applications to be seawater related. Duplex stainless steels have many uses in offshore oil and gas production and Naval equipment, particularly sub-surface.
Common duplex grades are: MTEK 2205, MTEK 29MN / CD4MCuN, Ferralium® 255, Zeron® 100
Precipitation Hardening (Age hardened) Stainless Steels
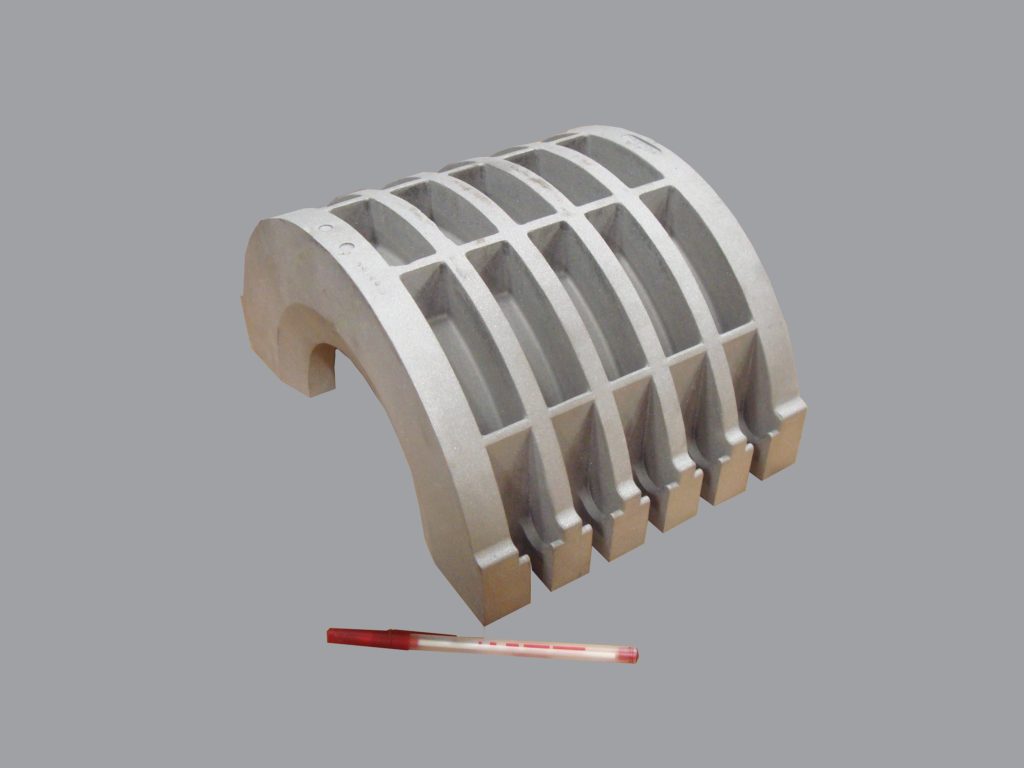
The need for stainless steels that would combine the excellent corrosion resistance of the austenitic types with the ability to be hardened by heat treatment led to the development of a family of stainless steels known as PH types. They can be precipitation (age) hardened by low temperatures (900°F / 480°C), minimizing distortion.
Common grades are: MTEK 17-4PH®, MTEK 15-5PH®, MTEK and 14-4PH®.
Applications of Ferrous Alloys in Key Industries
Ferrous alloys play a crucial role in a wide range of industries due to their strength, versatility, and specialized properties. Below are some of the key sectors where ferrous alloys are indispensable:
1. Power Generation
Ferrous alloys, particularly stainless steels and heat-resistant alloys, are essential for power generation equipment, including turbines, boilers, and heat exchangers. Their ability to withstand high temperatures and corrosion ensures long service life in demanding environments.
2. Oil and Gas
Duplex and super austenitic stainless steels are commonly used in offshore and subsea applications due to their resistance to corrosion and stress cracking. Components like valves, pumps, and piping systems rely on these alloys for durability in harsh, corrosive conditions.
3. Aerospace
Martensitic and precipitation-hardened stainless steels are used in aerospace for landing gear, structural components, and engine parts, where high strength and lightweight properties are critical.
4. Defense
Ferrous alloys are vital in defense applications, from armored vehicles and naval vessels to missile systems. Their strength, wear resistance, and toughness make them suitable for high-impact environments.
5. Medical and Food Processing
Austenitic stainless steels are extensively used in the medical and food industries due to their corrosion resistance and ease of sterilization. They are found in surgical instruments, food handling equipment, and chemical processing systems.
6. Automotive
The automotive industry uses various ferrous alloys for engine blocks, crankshafts, and suspension components, where strength and wear resistance are critical. Advanced high-strength steels are now common in vehicle body structures to improve safety and fuel efficiency.
Have questions? Contact the Metals Experts now.
Here is a resource on non-ferrous metals.