Blog What Is Aluminum Bronze? Is Aluminum Bronze An Alloy?
By: Dave Olsen
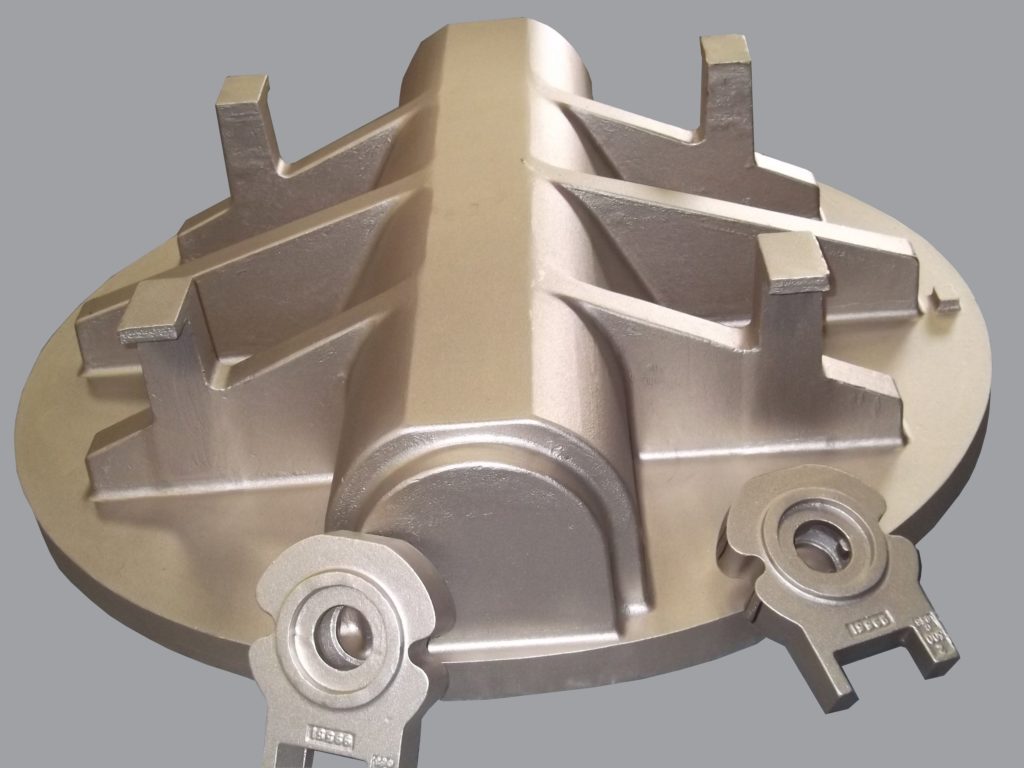
Aluminum Bronze alloys are a family of copper-based alloys that use iron and nickel in their chemistry but rely on aluminum as the principal alloying element. Aluminum significantly adds to the strength to the point that it is like that of medium carbon steel. The additional advantage is that aluminum bronze properties also include excellent corrosion resistance. It is that strength and corrosion resistance that gave rise to the early use of aluminum bronze.
A small adjustment in metallurgy causes significant changes in performance. This recognition of other properties has led to the use of Aluminum Bronzes for a variety of parts. Including parts requiring strength, hardness, resistance to wear and galling, low magnetic permeability, resistance to cavitation, erosion, softening, and oxidation at elevated temperatures. These aluminum bronze properties, together with ease of weldability, have greatly extended the fields of application for Aluminum Bronze.
Sustainability Advantages of Aluminum Bronze Alloy
As industries worldwide move towards more sustainable practices, the role of materials like Aluminum Bronze is gaining increased attention. Aluminum bronze alloys, with their outstanding durability, resistance to corrosion, and low maintenance requirements, can offer significant environmental benefits in comparison to other materials.
One of the main advantages of Aluminum Bronze in terms of sustainability is its long service life. Its high strength and resistance to wear and corrosion mean that components made from aluminum bronze typically last much longer than those made from other alloys, reducing the need for frequent replacements. This can lead to a reduction in waste and lower overall material consumption.
Additionally, Aluminum Bronze’s recyclability is another important factor in its sustainability. As a copper-based alloy, it can be recycled without significant loss of material properties, making it an ideal choice for industries focused on circular economy principles. The recycling of aluminum bronze requires significantly less energy than producing virgin materials, contributing to a lower carbon footprint.
Moreover, because of its corrosion resistance, aluminum bronze is widely used in marine and offshore environments. This capability reduces the need for coatings and chemicals often used in more reactive metals to prevent corrosion, further decreasing the environmental impact of such applications.
By choosing aluminum bronze, industries can not only benefit from a highly durable and performance-driven material but also align with sustainability goals and contribute to the reduction of their environmental footprint.
There are two major groups in the Aluminum Bronze family – Aluminum Bronze and Nickel Aluminum Bronze. Aluminum Bronze contains approximately 9-14% aluminum and 4% iron while Nickel Aluminum Bronze contains approximately 9-11% aluminum, 4% iron, and 5% nickel. That addition of nickel in the latter further improves the corrosion resistance of a material that is already strong in this area.
Common Aluminum Bronze alloys and some typical applications:
- C95200 is a highly ductile material with good corrosion resistance. This is ideally suited for bushings, bearings, light-duty gears, wear plates, low-pressure piping, pump columns, and containers.
- C95400 offers high yield and tensile strength, extraordinary toughness, and exceptional resistance to wear, fatigue, and deformation. This all-purpose alloy is widely used in chemical, marine, aircraft, and machine tools such as gears, bushings and bearings, pumps, and valves.
- C95500 is one of the toughest of the non-ferrous alloys. It serves the same industries as C95400 with higher strength, hardness, and corrosion resistance, though it has a slightly lower impact toughness.
- As a special Nickel Aluminum Bronze, C95800 is especially suited for marine applications with optimum resistance to seawater corrosion. Those may include propeller system parts, bushings, bearings, piping, including desalination, and other corrosive marine applications.
- C95900 provides higher hardness and compressive strength and is used for wear plates, forming rolls, draw dies, gears, valve guides, seats, and die inserts.
- MTEK 375 is an extremely hard, superior material often used for forming, drawing, and bending stainless steel.
Aluminum Bronze vs. Other Bronze Alloys: What Sets It Apart?
While aluminum bronze is a standout in terms of strength, corrosion resistance, and durability, it’s important to understand how it compares to other bronze alloys like tin bronze and manganese bronze. Each of these alloys offers unique properties suited to specific applications.
- Tin Bronze: Known for its excellent wear resistance and machinability, tin bronze is often used in applications that require friction resistance and long-term durability. While it offers good corrosion resistance, aluminum bronze generally outperforms tin bronze in harsh marine environments or under high-load conditions due to its superior resistance to corrosion and wear.
- Manganese Bronze: This bronze alloy is ideal for applications requiring high tensile strength and durability under high-pressure conditions. However, aluminum bronze surpasses manganese bronze in its resistance to cavitation, erosion, and corrosion, making it a more reliable choice for marine and high-performance industrial uses.
Aluminum bronze offers a unique combination of superior strength, exceptional corrosion resistance, and long-lasting performance in challenging environments, making it the ideal choice in industries like aerospace, marine, and chemical processing.
For guidance in selecting the appropriate aluminum bronze in your application, contact us.