Blog What Is The Continuous Casting Process?
By: Dave Olsen
Overview of Continuous Casting
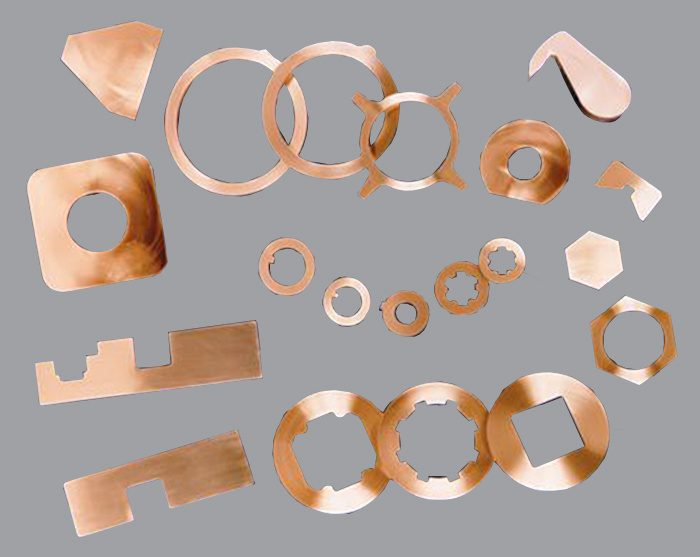
Continuous cast shapes are produced by introducing molten metal into a vertical or horizontal mold that has the ability for rapidly chilling the metal to the point of solidification. The rapid chilling in the mold ensures a fine, uniform grain structure in the solidified metal with higher physical properties than sand castings. Once solidified, the cast shaped bar is cut to the desired length.
The most common continuous casting shapes produced are tubes and solids. However, other continuous casting shapes such as square, rectangular, hexagonal, and many other irregular shapes can also be produced to match a desired finished part profile.
Continuous Casting Process Details
Molten metal from an induction furnace is fed directly
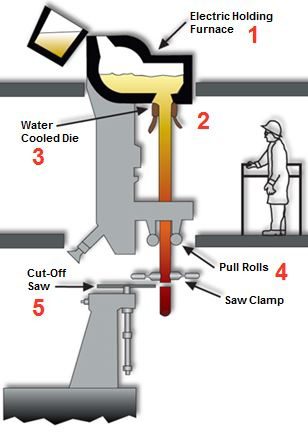
into a mold with the required shape (1). The molten metal enters the die through a series of holes in the upper portion of the mold. Heat is extracted by the water-cooled jacket surrounding the mold, and the metal solidifies. The molten metal above the die acts as a riser keeping the die filled and preventing the formation of shrinkage cavities in the required finished form: bar, tube or special shape (2).
Solidification occurs in the die and then the solidified metal casting exits through the bottom of the die by means of a continuous process of short intermittent extractions performed by a mechanical device (3).
The product is withdrawn at controlled increments and speed until the production length is met (4). Lengths are cut off by a traveling saw which moves with the cast shape. The standard length for continuous cast material is 144 inches (5).
Since continuous casting operates as a true gravity fed bottom-flow casting method, the process minimizes the possible trapping of casual dirt and dross in the casting. Foreign matter in the furnace crucible floats to the top of the melt so it does not become part of the cast product.
Low casting temperatures combined with the chill mold and directional solidification inherent in this process promote a homogeneous, fine-grained, high-density product with high yield.
A horizontal method of continuous casting has also found some favor in the foundry industry. The principle is basically the same as it is for the vertical method, except the equipment stretches out horizontally and is contained on one level. Tube hollows produced by the horizontal method require somewhat more stock allowance to compensate for the natural effect of gravity on ovality and straightness.
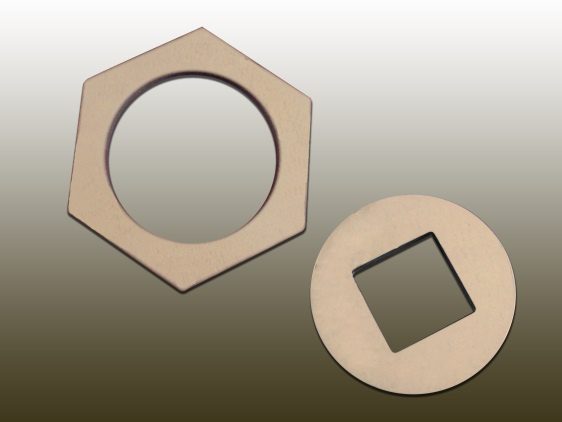
Shapes other than solid round bar and tube hollows are routinely cast by either method. Rectangular, hexagonal, square, gears with teeth, and a multitude of other shapes lend themselves to the continuous cast method. This method is excellent for producing small inside diameters.
Continuous cast products can offer cost advantages over other types of casting if the optimum quantity, shaping, and sizes are chosen.
Advantages of Continuous Casting
- Ability to cast regular shapes and certain irregular configurations in long tubular form, which is difficult for other casting methods.
- Continuous cast bars require appreciably less machining stock.
- Continuous cast material is consistently dense and homogeneous in structure, and therefore well-suited for pressure applications.
- Straight, true, and concentric product for high speed bar machines.
- Many suppliers maintain stock sizes for ready availability to distributors and others requiring full lengths.
- If the shape is optimized, the clean-up stock required on continuous cast material is often less than that needed for parts produced with other casting processes. Stock of 1/32 to 3/32 inches per side depending on the casting size is normally adequate.
- Continuous castings have an inherent advantage in mechanical properties over other methods because of the chilling and the excellent feeding of molten metal during solidification.
- Continuous castings perform well under pressure.
Limitations or Things to Consider
- Due to the considerable mold cost and casting machine set-up, it is uneconomical to consider the continuous cast method for special shapes or special alloys in small quantities. A customer may need to order over 2,000 pounds of a special size or special alloy in order to obtain a reasonable cost.
To learn more about this process or to determine if it is a fit for your application, please contact us.