Blog What Is Tin Bronze?
By: Dave Olsen
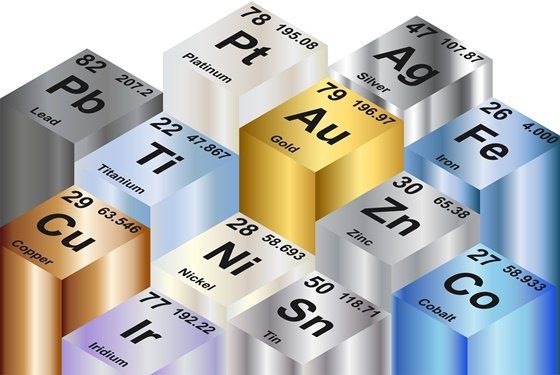
Tin Bronze alloys consist of copper-based materials with the major alloying element being tin. The presence of tin provides high mechanical properties, the offset being that the addition of tin adds to the metal cost. The high tin bronzes, however, are particularly suited for certain applications for which the less expensive bronzes are not suitable.
The variations in chemistry, particularly the addition of lead, are primarily designed to enhance machinability characteristics and pressure tightness.
MTEK 65 / C90700 (which is 89% copper and 11% tin) is a typical High Tin Bronze. Bronzes containing high tin content possess stronger mechanical properties. This bronze is used for gears, bearings, bushings, pump bodies, and structural parts.
Other tin bronzes serve similar applications:
- MTEK Tin Bronze / C90500 (87% Copper, 10% Tin, 2% Zinc, + others)
- MTEK Navy G 1% Lead / C92300 (87% Copper, 8% Tin, 4% Zinc, 1% Lead)
- MTEK 87-11-0-1 / C92501 (87% Copper, 11% Tin, 1% Nickel, 1% Lead)
- MTEK Leaded Tin Bronze / C92700 (87% Copper, 10% Tin, 2% Led, 1% Nickel)
Their uses include heavy load, low speed service applications. These alloys are the premier gear alloys for long life under heavy loads. They are used for piston pin and linkage bushings, valve guides, and many types of bearings including rolling mill, worm, and pilot for the machine tool industry. They are also used for steam fittings, impellers, and seal rings. Alloys in this group are particularly resistant to corrosion caused by certain specific materials.
In general, these alloys can operate as bearings at maximum temperatures up to 500°F / 260°C and loads of 4000 lbs. per square inch. Bearings of these alloys, however, must be very carefully aligned and positively lubricated, and they require harder shafts than do the high leaded bronzes.
For guidance in selecting the appropriate tin bronze in your application, contact us.