Blog Why Certain Metals Offer Greater Wear Resistance
By: Dave Olsen
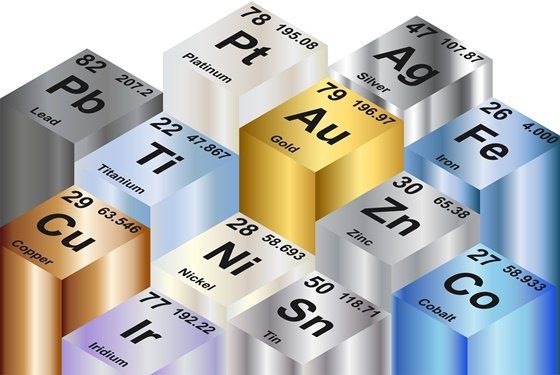
One regularly hears recommendations about material selection. Use this alloy for superior heat resistance. Or that for seawater corrosion. Or this other one for a high wear application. But what about the alloy actually makes it deliver that performance?
In this installment, we will explore some simplified technical reasons – at the microscopic level – why certain metals inherently offer greater resistance to wear.
First, a definition of “wear.” In our context, we will define wear as the loss or deformation of a metal that is the result of the mechanical interaction with another material (not necessarily metal). Wear may take a number of forms including abrasion, adhesion or galling, erosion, and spalling. It is highly impacted by product design and installation. The rate and types of wear can also be affected by temperature and the fluid environment. Wear is often measured as the amount of mass that is lost in a given period.
Why do some metals resist wear?
In actual applications, it is simplistic to ignore the relative impact of component size and shape, surface finishes, the angle of mating parts, load, speed, and the like; but we will save those design discussions for another day. At a more basic level, materials that have a high level of hardness tend to wear better, especially when mated with a softer material. A lot of a material’s hardness has to do with its micro-structure, both on the surface and sub-surface.
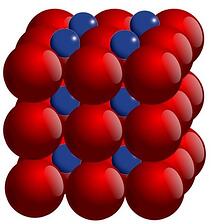
On a microscopic scale, metals are made up of an arrangement of atoms and molecules that form a lattice geometry. Managing the ability of atoms to move within this lattice plays a large role in controlling the strength, ductility and wear properties of metals. Atoms move with the aid of small irregularities within the lattice; those irregularities are called dislocations.
Dislocations serve as openings in the lattice for the atoms to move into as the dislocation proceeds through the lattice. When dislocations are prevented from moving, the atoms are not able to move and the metal is generally harder and stronger. And as we have noted, harder metals tend to provide better wear properties.
How do we keep the atoms from moving?
That is where alloying comes into play.
The atoms of added alloys that are larger or smaller than those in the existing matrix hinder the movement of dislocations through the lattice. Less movement means harder and stronger, which generally means better wear. Conversely, adding alloys whose atoms are similar in size to the ones already in the matrix do not discourage dislocation movement and the impact on properties is minimal.
Certain elements like carbon feature very small atoms that fit within the matrix; others are too large and replace atoms within the matrix. When these substitutional (alloying) atoms are significantly different in size than the matrix atoms, dislocations are discouraged, and strength and wear resistance is generally enhanced.
The expected impact of the addition of certain metal alloying additions is well understood. For example, tin is added to bronze to add strength; gear bronzes generally contain 10% or 12% tin. The addition of zinc also adds strength, but if too much zinc is added, anti-friction properties are reduced. Aluminum is added as an alloy to increase strength and performance at higher temperatures, but attention must be paid to the offsetting loss of ductility. Different alloys respond better to certain lubrication types and some can perform adequately for a time (those including lead, for example) in the absence of lubrication.
It is not sufficient to consider hardness alone when selecting a material for an application demanding high resistance to wear. But understanding that the microstructure of the material, and the addition of alloying elements that contribute to that, help drive a cost-effective alloy selection decision for wear resistance.