Blog Will Aluminum Rust or Corrode?
Aluminum does not rust but it can corrode. What is the difference between rust and corrosion? Rust and corrosion, while often used interchangeably, represent distinct phenomena. Corrosion is the broader term, referring to the gradual degradation of metal through chemical reactions. On the other hand, rust refers to the oxidation of iron-based alloys like steel, brought about by exposure to moisture or water.
Since aluminum doesn’t contain iron, it doesn’t rust away in most conditions. However, aluminum can corrode when exposed to moisture and oxygen. This process, called oxidation, leads to the formation of a white layer over the affected aluminum, which acts as a protective shield against further corrosion.
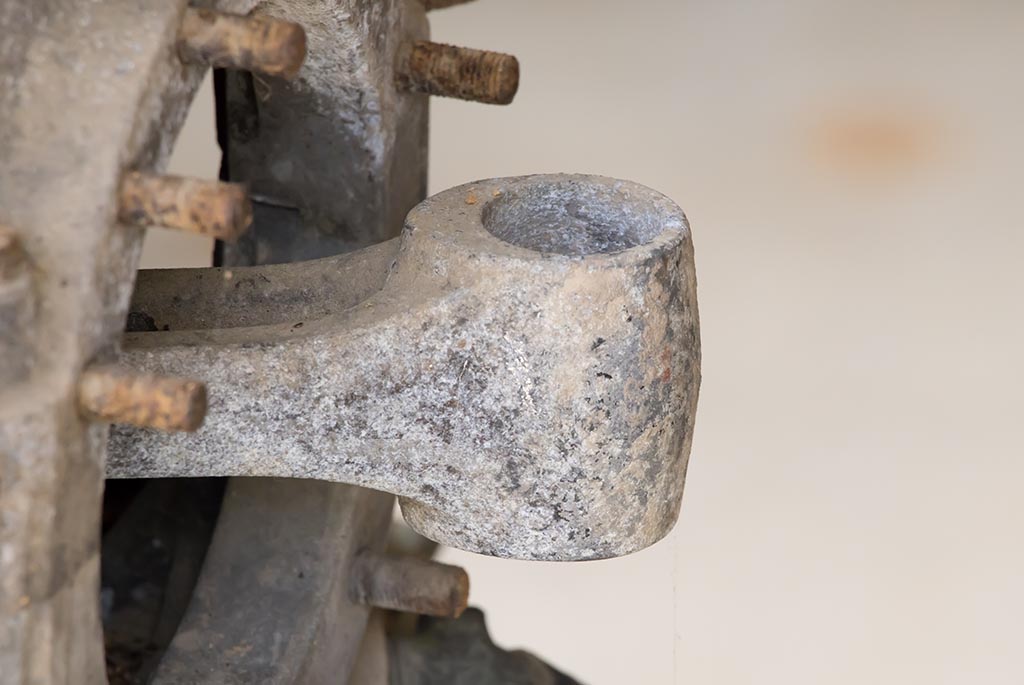
Should I Choose Aluminum Or Stainless Steel For My Project?
Selecting between aluminum and stainless steel hinges on a multitude of factors, ranging from longevity and heat tolerance to strength requirements. Both materials serve a broad spectrum of applications with their unique properties. While aluminum boasts a superior strength-to-weight ratio, it may require additional treatments like painting or anodizing to attain desired characteristics. In contrast, stainless steel often provides the desired properties without further enhancements, making it a better fit for heavy-duty and high-heat projects.
Stainless Steel For Superior Corrosion Resistance
Stainless steel is the embodiment of corrosion resistance. This alloy is primarily composed of iron, chromium, and nickel, and its name reflects its remarkable ability to resist rust. When exposed to environmental elements, stainless steel forms a protective chromium oxide layer, acting as a fortress against the effects of corrosion. Its intrinsic properties make it an unparalleled choice in various applications, from culinary utensils to architectural marvels, and even in the demanding environments of chemical and petrochemical industries.
The Unrivaled Properties of Aluminum
Aluminum, often known for its lightweight nature, also boasts good resistance to corrosion. Though it lacks the “steeliness” of stainless steel, aluminum’s inherent anti-corrosion qualities make it a preferred choice in construction, aerospace, and transportation sectors. The formation of an aluminum oxide layer when exposed to air is the guardian that shields this metal from rust’s grasp. Aluminum’s resistance is particularly crucial in applications where weight reduction is vital, such as aircraft and automotive manufacturing.
Crucial Differences Between Stainless Steel And Aluminum
Depending on your application and requirements, stainless steel may be a better fit. Let’s evaluate a few key differences between stainless steel and aluminum.
Corrosion Resistance:
Both aluminum and stainless steel offer corrosion resistance. Stainless steel will typically perform better depending on the environment. It’s worth noting that chlorides and sulfides will corrode aluminum quickly. Stainless steel’s corrosion resistance and rust resistance makes it highly versatile in a range of industries.
Heat Resistance:
Stainless steel offers better heat resistance than aluminum. Stainless steel is resistant up to 2500℉ (1371°C) but aluminum is up to only 400℉ (204°C). However, in colder temperatures aluminum’s strength increases and stainless steel becomes more brittle.
Strength vs. Weight:
Stainless steel has a clear strength advantage over aluminum. It is simply denser and stronger. Interestingly, aluminum has a better strength-to-weight ratio. Aluminum typically weighs 1/3 of steel. Strength to weight is an important factor for certain applications like aerospace.
Malleability:
Aluminum is ductile and easy to machine. It is softer and easier to stretch and bend. Stainless steel is easy to machine depending on experience but does take longer.
Cost:
For metal cast parts, stainless steel will likely cost more depending on the size, shape, specific alloy used, and current metal prices. Stainless steel offers a better price based on weight, due to density. On the other hand, aluminum is a better option based on volume.
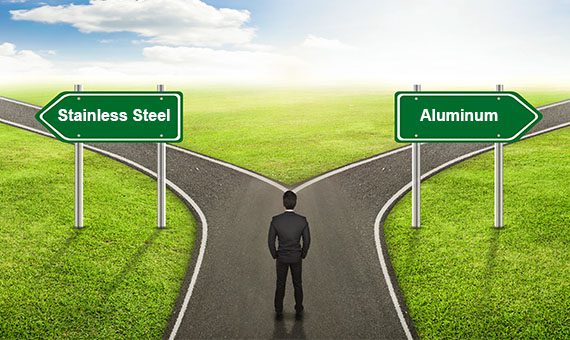
What Applications Are A Better Fit For Stainless Steel?
- Gears
- Shaft sleeves
- Petrochemical tubes and fittings
- Food & beverage process equipment
- Chemical & pharmaceutical processing equipment
- Furnace rolls
- Pressure vessels
What Applications Are A Better Fit For Stainless Steel?
- Automotive components
- Gear boxes
- Housings
- Heat sinks
- Aerospace parts not exposed to high heat
Stainless Steel Vs. Aluminum: The Bottom Line
Stainless Steel Advantages:
- Excellent strength
- High heat resistance – up to 2500℉ (1371°C)
- Non-corrosive
Aluminum Advantages:
- Low density – lightweight
- Easy to machine
- Will not rust
How to Prevent Corrosion in Aluminum and Stainless Steel
Proper maintenance and material selection are essential for prolonging the life of aluminum and stainless steel components. Here are some steps to mitigate corrosion:
Tips for Preventing Aluminum Corrosion
- Anodizing or Coating: Apply an anodized finish or protective coating to shield aluminum from moisture and harsh environments.
- Avoid Contact with Chlorides: Keep aluminum away from saltwater or chloride-rich environments to minimize corrosion.
- Regular Cleaning: Remove dirt and contaminants to prevent pitting corrosion.
Tips for Preventing Corrosion in Stainless Steel
- Select the Right Alloy: For high-corrosion environments (e.g., marine or chemical exposure), opt for stainless steel grades with higher chromium or molybdenum content, such as 316 or duplex stainless steel.
- Maintain the Protective Layer: Regular cleaning helps maintain the passive chromium oxide layer, enhancing corrosion resistance.
- Avoid Galvanic Corrosion: Prevent contact with dissimilar metals to reduce the risk of galvanic corrosion.
In the stainless steel vs. aluminum conundrum, the decision hinges on your specific project requirements. Each material offers distinct advantages, whether it’s stainless steel’s superior strength or aluminum’s lightweight versatility. MetalTek stands ready to assist you in determining the ideal alloy for your project, building a lasting partnership to ensure the perfect fit is achieved.
While MetalTek doesn’t pour aluminum, we’ll steer you toward the right choice for your application, be it stainless steel or aluminum, and ensure that it stands up to the test of time. Feel free to contact us today to discuss your application.