Metal Testing & Analysis
Our Quality Metal Testing Ensures The Safety Of Others
MetalTek produces components that simply can never fail. Our quality ensures the safety of both our customers and end users in highly demanding markets such as aerospace, defense, and petrochemical. There are potential issues that can arise during the metal casting process. Having a sound procedure helps, but having the testing ability is critical to any metal casting project. MetalTek facilities have extensive metal testing and metal analysis capabilities. We feature on-site mechanical testing, chemical analysis, dimensional testing, and non-destructive testing (NDT). MetalTek also offers metallographic testing. At the end of the day, we provide components that meet exact customer specifications and are certified to the highest quality standards.
Mechanical Testing
MetalTek can meet a range of mechanical requirements through comprehensive mechanical testing capabilities. Our certified technicians push the mechanical limits of our components to ensure they meet the highest quality and safety standards. The benefit of mechanical testing is a numerical value is provided along with it typically being non-destructive. Our metal mechanical testing capabilities include:
-
Tensile testing (ambient and elevated temperatures)
-
Impact testing / Charpy
-
Brinell & Rockwell hardness testing
-
Stress rupture
Chemical analysis
MetalTek performs a range of chemical analysis techniques to confirm the chemical composition of the components we produce. Chemistry composition is likely the most common metal casting quality test available. Through our various chemical analysis tests, MetalTek can determine the quality of materials and which alloys could be at fault. Our chemical analysis tests include:
-
Carbon sulfur determinator
-
Chemical analysis using optical emission spectrometers
-
Phase examination
-
X-ray fluorescence (spectrometer)
Dimensional Testing
MetalTek uses several testing methods to confirm that the dimensions of the components we produce are consistent with the strictest customer quality standards. This type of metal testing is primarily visual and does not physically affect the component. Typically, a dimensional test is utilized on engine parts, valves, or higher-priced metal casts. Our dimensional testing methods include:
-
Visual inspection
-
Standard metrology with standards traceable to NIST
-
Coordinate-measurement machine (CMM) – by far the most accurate measurement
-
Laser scanning for dimensional compliance inspection
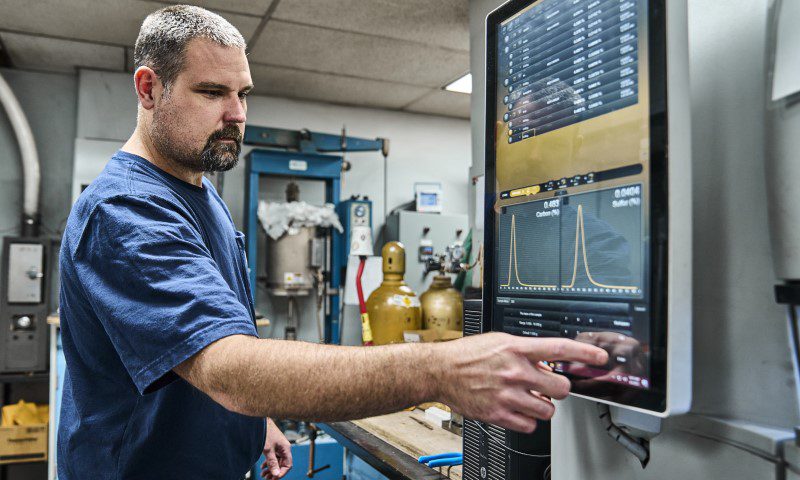
Non-Destructive Testing (NDT)
Multiple MetalTek facilities are independently audited and certified to Nadcap and other NDT standards. Instrumentation is fully calibrated to industry standards. On-site technicians are fully trained and certified in NDT Level II and III. MetalTek NDT capabilities include:
-
Fluorescent penetrant inspection (FPI) / liquid penetrant inspection (LPI)
-
Magnetic particle inspection
-
Online and offline hydrostatic testing
-
Positive material identification
-
Radiography (x-ray)
MetalTek utilizes a digital laboratory information management system (LIMS) to compare test results against a database of customer specifications. The LIMS helps to track data over time to improve efficiency and support compliance efforts.
Our comprehensive metal testing and analysis capabilities include mechanical testing, dimensional testing, chemical analysis, and non-destructive testing. Check out our comprehensive guide on metal casting inspection methods and what they tell us and what the limitations are. No matter the metal casting requirements, MetalTek ensures that the most rigorous project specifications are met.