Centrifugal Casting
Need help with a new project?
Let's push the limits of what is possible, together. Ask your metal experts.
What is Centrifugal Casting?
Centrifugal casting is the preferred metal casting process for applications demanding high strength and reliability, such as flight and land-based turbine engine compressor cases, petrochemical furnace tubes and reformer tubes, and naval defense components. Centrifugal casting produces defect-free parts with excellent material integrity.
In centrifugal casting molten metal is poured into a spinning die, which rotates on a vertical or horizontal axis depending on the part's design. Vertical centrifugal casting is commonly used for rings and cylinders, while horizontal centrifugal casting is ideal for tubes. Each can yield multiple parts from a single casting, increasing efficiency.
Intense centrifugal force pushes denser metal to the outer diameter (O.D.) and drives impurities and oxides toward the inner diameter (I.D.), where they can be removed by machining. Directional solidification under pressure ensures a uniform structure, preventing mid-wall shrinkage and eliminating defects such as gas pockets or cavities.
Our Centrifugal Casting Expertise
MetalTek produces ferrous and non-ferrous centrifugal castings at our Sandusky International and Wisconsin Centrifugal Divisions. Our industry-leading centrifugal casting capabilities cover a wide range of sizes and are supported by the world’s largest and most diverse inventory of centrifugal casting dies. For customers, this minimizes upfront tooling costs and reduces lead times.
-
Horizontal centrifugal castings: O.D. up to 60 in. (1525 mm), length up to 432 in. (10 973 mm), and weight up to 125,000 lbs. (56 700 kg)
-
Vertical centrifugal castings: O.D. up to 180” (4572 mm) and weight up to 34,000 lbs. (15 422 kg)
Centrifugal Casting Video
When to Use Centrifugal casting
Centrifugal casting is a good choice when your application requires:
-
Symmetrical shapes such as tubes, rings, and cylinders
-
Improved material properties over sand casting
-
Eliminating centerline shrinkage to improve structural integrity
-
Limited I.D. features
-
Large parts up to 125,000 lbs. (56 700 kg)
-
Uniform grain structure for enhanced strength and performance
-
High dimensional integrity for applications such as defense
Solutions
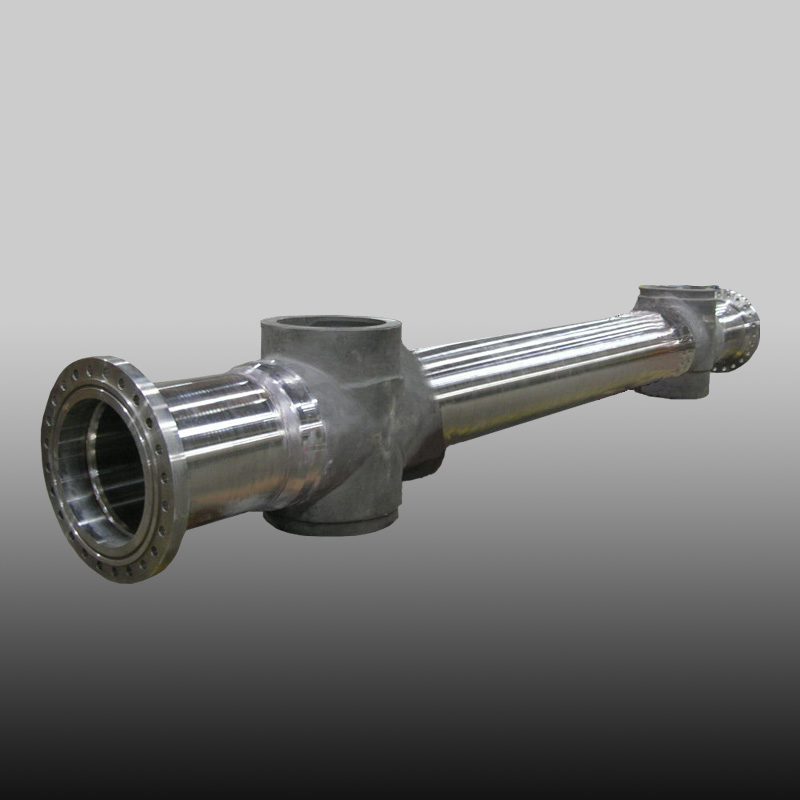
Alternative Fuel Assembly
Capability to fabricate heavy wall assemblies for alternative fuel roduction
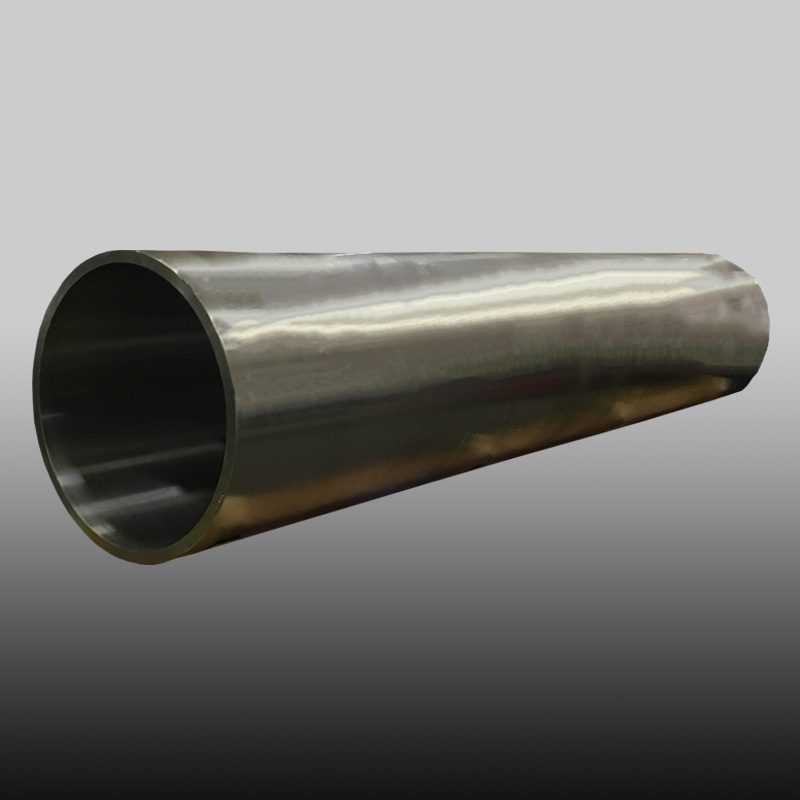
Shaft Sleeves
Propulsion shafting for ocean-going Military and Commercial vessels is a critical and expensive part of the propulsion system.
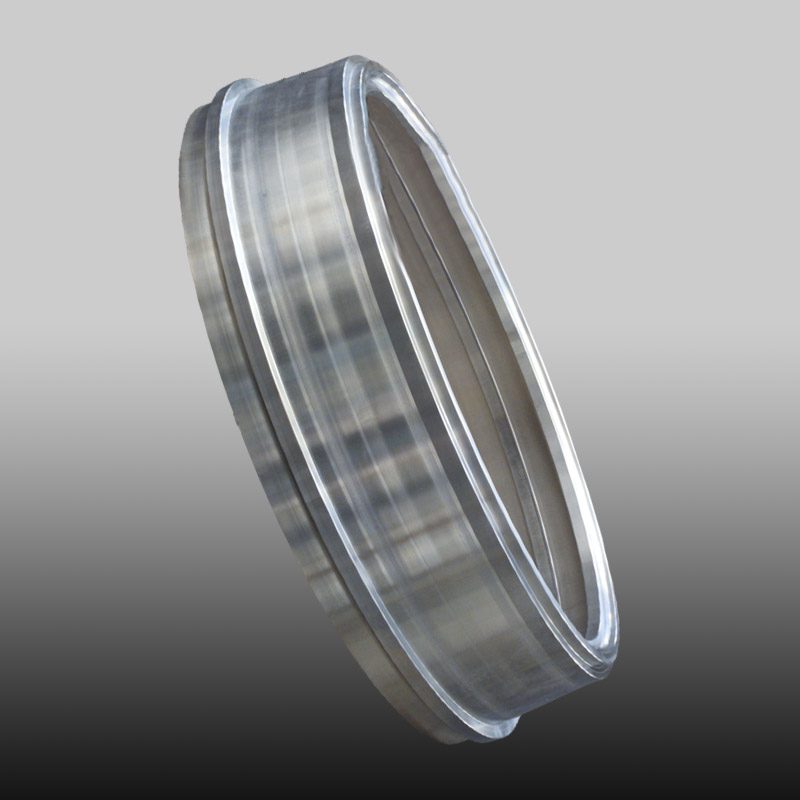
Tooling Mandrel
Centrifugally cast tooling can provide 5 times longer tool life than traditional fabricated assemblies.